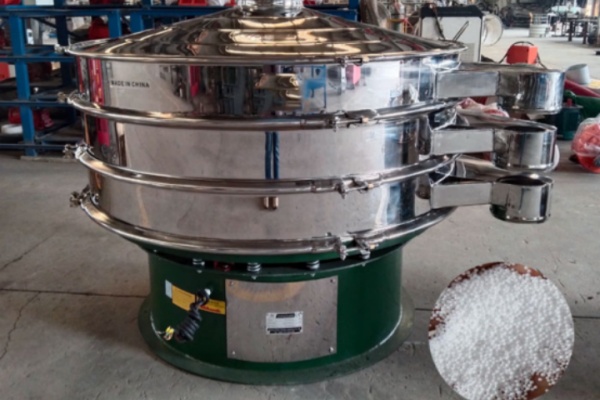
Sieve For Polystyrene Pellets
Sieve for polystyrene pellets generally ranges in price from $800.00-$6000.00/Set.There are a variety of models to choose from, typically categorized by sieve diameter (such as 300mm, 450mm, 600mm) and mesh density.
Screening mesh: 1-500 mesh
Layer: 1-5 layers
Production: 0.5-5000kg/h
Model selection: Standard type, flanged type, explosion-proof type, ultrasonic type
What is Sieve For Polystyrene Pellets?
Sieve For Polystyrene Pellets is used for precise classification and impurity removal of polystyrene (PS/EPS) particles. Its core function is to efficiently separate polystyrene particles of different particle sizes and remove impurities (such as fine powder, lumps or foreign matter in polystyrene) through three-dimensional vibration to ensure product uniformity and purity; it can screen polystyrene particles of 20 mesh (0.84mm) to 500 mesh (0.028mm), including the screening of new material granulation and recycled crushed materials. The output of a single machine is 0.5~5 tons/hour, the screening efficiency is >95%, and the fully enclosed structure prevents dust and reduces consumption. The bouncing ball or ultrasonic net cleaning design effectively solves the problem of net blocking caused by electrostatic adsorption of polystyrene, ensuring continuous production.
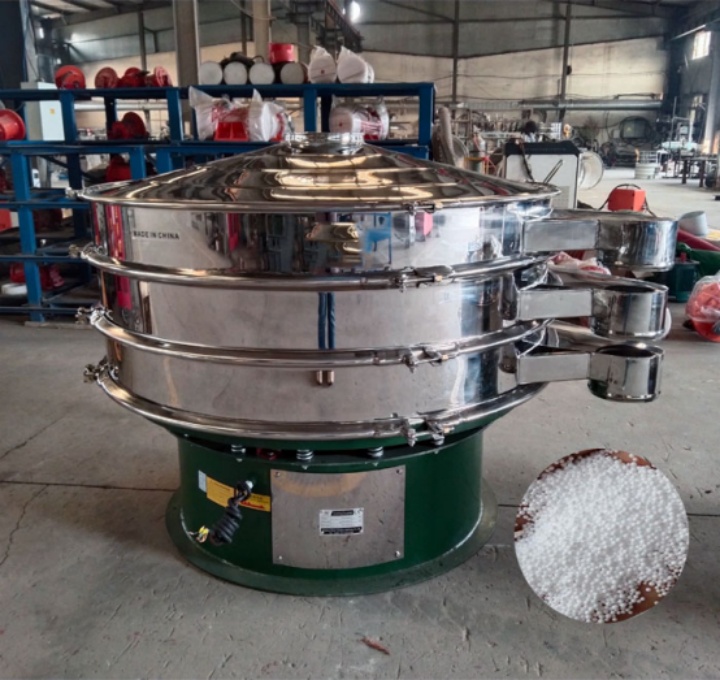
What types of Sieve For Polystyrene Pellets are there?
Sieve For Polystyrene Pellets provides standard, flanged valve, explosion-proof and ultrasonic models according to different requirements of polystyrene particle processing volume and screening accuracy:
Standard Sieve For Polystyrene Pellets: diameter is 600mm-2000mm, with 1-5 layers of screen (3 layers are the best), processing capacity is 0.5-5 tons/hour (specific output depends on the particle size), which can be used for particle size classification and impurity removal of conventional polystyrene particles
Flanged valve type Sieve For Polystyrene Pellets: adopts enlarged feeding port + adjustable discharge valve, which can control the retention time of the screened material through the valve to improve the screening accuracy, suitable for high viscosity or easy to accumulate modified polystyrene particles.
Explosion-proof Sieve For Polystyrene Pellets: adopts explosion-proof motor + full grounding design, which can handle polystyrene fine powder containing static electricity.
Ultrasonic Sieve For Polystyrene Pellets: Install an ultrasonic screen cleaning system to prevent mesh clogging. It can be used for screening high-mesh (400 mesh or more) polystyrene micropowders, with a minimum of 5 microns.
What are the advantages of Sieve For Polystyrene Pellets?
Sieve For Polystyrene Pellets can efficiently screen the characteristics of polystyrene particles, accurately classify, quickly change the net in 3-5 minutes, seal and dust-free, and the screening accuracy can reach 95%.
Efficient screening: Using a unique three-dimensional vibration principle, the screening efficiency is 30%-50% higher than that of ordinary vibrating screens, especially suitable for lightweight materials such as polystyrene particles.
Designed for polystyrene characteristics: The screen frame is made of wear-resistant nylon or stainless steel to avoid static electricity generated by friction with polystyrene particles. The special sealing structure prevents fine powder leakage, meets the environmental protection requirements of the plastics industry, and the bouncing ball is made of food-grade silicone to avoid contamination of materials.
Precise grading: can accurately screen polystyrene particles of 20-500 mesh (0.028mm-0.85mm), meeting the strict requirements of different industries for particle size
Quick screen change: patented mother-child screen separation design, screen replacement only takes 3-5 minutes, greatly reducing downtime and improving production efficiency
Dust-free and environmentally friendly: fully enclosed structure design, polystyrene particles do not fly during screening, meet environmental protection requirements, and improve the working environment.
Parameters of Sieve For Polystyrene Pellets
Model |
Diameter (mm) |
Feeding Size (mm) |
Frequency (RPM) |
Layers |
Power (kw) |
Capacity (kg/h) |
DH-400 | 400 | <10 | <1500 | 1-5 | 0.18 | 100 |
DH-600 | 600 | 0.25 | 200 | |||
DH-800 | 800 | 0.55 | 500 | |||
DH-1000 | 1000 | 0.75 | 800 | |||
DH-1200 | 1200 | 1.1 | 1200 | |||
DH-1500 | 1500 | 1.5 | 1800 | |||
DH-1800 | 1800 | 2.2 | 2000 |
What is the working principle of Sieve For Polystyrene Pellets?
When Sieve For Polystyrene Pellets is working, polystyrene particles enter the sieve from the feed inlet. Under the action of the vibration motor, the polystyrene particles make horizontal, vertical, and inclined three-dimensional movements on the screen surface, and quickly spread to the surroundings. Polystyrene particles smaller than the sieve hole pass through the sieve and become undersize, and particles larger than the sieve hole move along the sieve surface to the discharge port for discharge.
What is the role of Sieve For Polystyrene Pellets?
Sieve for polystyrene pellets plays a crucial role in the processing of polystyrene particles, primarily functioning to classify particles by size and remove impurities, thereby ensuring the quality and uniformity of the final product.
Particle classification: The polystyrene mixed particles can be classified according to the target size. One device has 1-5 layers to choose from, and the particles can be screened into 2-6 specifications to ensure the uniformity of the finished particles.
Particle removal: Efficiently separate foreign matter (such as label fragments, metal chips, sand and gravel) from polystyrene particles, especially for the complex composition of recycled crushed materials, which can improve the purity of the finished particles.
Sieve For Polystyrene Pellets can be used for screening new material granulation particles, recycled crushed materials and expanded particles (EPS) with a particle size of 0.028mm (500 mesh) to 60mm. It is often used in the final screening of new material production lines, recycling and impurity removal of recycled materials, and pre-treatment of EPS pre-foaming, accurately and efficiently solving the needs of polystyrene particle classification and purification processes.
Analysis of screening results
Model | C-102 | C-103 | C-104 | C-105 | C-106 | C-107 | C-108 |
---|---|---|---|---|---|---|---|
Bead Size (mm) | 1.40-2.00 | 1.00-1.60 | 0.85-1.25 | 0.70-1.00 | 0.50-0.80 | 0.40-0.60 | 0.30-0.50 |
Foam Density (g/L) | 14-20 | 10-12.5 | 11-14 | 12.5-13 | 13-18 | 25-33 | 18-50 |
Sieve Analysis Efficiency | 95% | 95% | 95% | 95% | 95% | 95% | 95% |
Pentane Content | >6% | >6% | >6% | >6% | >6% | >6% | >6% |
Residual Monomer | ≤0.3% | ≤0.3% | ≤0.3% | ≤0.3% | ≤0.3% | ≤0.3% | ≤0.3% |
Moisture Content | ≤1.0% | ≤1.0% | ≤1.0% | ≤1.0% | ≤1.0% | ≤1.0% | ≤1.0% |
What are the applications of Sieve For Polystyrene Pellets?
Sieve For Polystyrene Pellets can be used for screening new material granulation particles, recycled crushed materials and expanded particles (EPS) with a particle size of 0.028mm (500 mesh) to 60mm. It is often used in the final screening of new material production lines, recycling and impurity removal of recycled materials, and pre-treatment of EPS pre-foaming, accurately and efficiently solving the needs of polystyrene particle classification and purification processes.
Sieve For Polystyrene Pellets Customer Case
Customer Cases | Application Scenarios | Screening Mesh | Output | Recommended Models |
Taiwan EPS Manufacturer | EPS Foam Bead Grading (Removing Agglomerates/Deformed Particles) | 100 Mesh (0.15mm) | 1.5-2.5 tons/hour | DH-1200 |
A food processing plant in Europe | Recycled PS granules impurity removal (labels/metal chips) | 100 mesh + 120 mesh double-layer screen | 0.8-1.2 tons/hour | DH-800 stainless steel |
A modified plastics factory in Southeast Asia | Carbon fiber composite PS granules powder removal (anti-oxidation) | 200 mesh (0.074mm) | 1.0-1.8 tons/hour | Customized (nitrogen protection) |
Shanghai Plastic Recycling Company | Recycled PS crushed material classification (sorting 0.5-3mm) | 20-60 mesh multi-stage sieve | 3.0-5.0 tons/hour | DH-1000 |