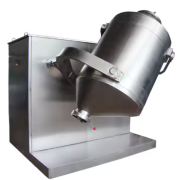
Three-dimensional motion mixer
The three-dimensional motion method is used to enable the material to flow, diffuse and dope in multiple directions during the mixing process, ensuring that the mixing uniformity can reach more than 99%.
Maximum loading capacity: up to 60% of the total volume of the mixing barrel
Applicable materials: suitable for materials with large mixing ratio differences or requiring fine and uniform materials
Highlights of the three-dimensional motion mixer
①Can achieve a mixing uniformity of ≥99% in a relatively short time
②No damage to the material, no stratification
③No dead angle mixing in three-dimensional space
What is a three-dimensional motion mixer
Three-dimensional motion mixer is a powder device that uses multi-directional composite motion of materials in three-dimensional space to achieve efficient mixing. It is mainly composed of a drive system, a mixing barrel, a frame and a control system. The mixing barrel simultaneously performs multi-directional movements such as up and down, front and back, left and right during operation, so that the material in the barrel is constantly flipped, diffused and convected, thereby achieving a fast and uniform mixing effect. The equipment has no stirring blades, and the material is not affected by centrifugal force. It is suitable for mixing powders or particles with large differences in particle size and density, especially for application scenarios with protection requirements for particle structure.
Comparison of the advantages of three-dimensional motion mixers and traditional mixers
Comparison items |
three-dimensional motion mixer |
traditional mixer (such as V-type, double cone, trough type) |
Picture |
|
|
Mixing method |
multi-directional (three-dimensional space) compound motion |
single-axis or double-axis rotation, or mechanical stirring |
Mixing uniformity |
high, generally up to ≥99% |
high, but prone to dead corners, slightly lower uniformity |
Filling factor |
high, up to 60% of the cylinder volume |
medium, generally 30%–50% |
Applicable materials |
powders, particles, large weight ratio differences, fragile materials, etc. |
ordinary powders, homogeneous particles |
Material damage degree |
extremely low, suitable for fragile materials that need to protect the structure |
some stirring or shearing may damage the particle structure |
Mixing time |
short, generally 5~15 minutes |
relatively long, may take more than 15~30 minutes |
Working principle of three-dimensional motion mixer
The working principle of the three-dimensional motion mixer is based on precisely controlled three-dimensional motion. It usually consists of a base, a drive system and a universally suspended mixing container (barrel). Through clever mechanical structure design, such as the driving shaft, driven shaft, fork and hinge point, the mixing container can perform the following three complex movements at the same time during the movement:
Translation: The mixing container moves as a whole in space.
Rotation: The mixing container rotates around its own axis.
Turning: The mixing container tilts and overturns in space.
The superposition of these three movements makes the materials in the container fully stirred and dispersed in all directions, avoiding the dead angle and stratification that may occur in traditional mixers. The materials are constantly diffused, convected and sheared in the container, thereby achieving a very high degree of mixing uniformity.
Structural composition of three-dimensional motion mixer
Machine base: It plays the role of supporting the entire equipment. It is generally made of solid materials such as carbon steel or stainless steel to ensure the stability of the equipment during operation.
Transmission system: It consists of a motor, a transmission reduction system, a frequency converter, etc. The motor provides power, and the transmission reduction system converts the high-speed rotation of the motor into a speed suitable for the movement of the mixing barrel. The frequency converter can effectively buffer the inertia of heavy-load startup, and can also accurately select the best position of the barrel when it stops to facilitate feeding or discharging.
Electrical control system: used to control the start, stop, speed adjustment and other operations of the equipment. It is usually equipped with an operation panel to achieve precise control of the mixing process. Some advanced control systems also have fault diagnosis and alarm functions.
Multi-directional motion mechanism: It is designed with a unique active and driven dual-axis and two-axis end three-dimensional motion rocker arm structure. The driven axis is designed to be flexible, making the machine more flexible and light, and more convenient for debugging and maintenance. The three-dimensional motion rocker arm mechanism is made of all stainless steel and polished, and can be used in clean areas.
Mixing barrel: It is in direct contact with the material and is generally made of stainless steel. The inner and outer walls of the barrel are polished. The large arc octahedral barrel design makes the material move without slipping and can guide the material to roll immediately. The mixing barrel consists of a barrel body, a positive cone feed end, an eccentric cone discharge end, a feed port and a discharge device.
Common model parameters of three-dimensional motion mixer
Model |
Effective volume (L) |
Loading volume (L) |
Maximum loading weight (kg) |
Main motor power (kw) |
Drum speed (r/min) |
Total machine weight (kg) |
SYH-5 |
5 |
3 |
2 |
0.25 |
0–20 |
60 |
SYH-100 |
100 |
60 |
40 |
1.5 |
0–15 |
300 |
SYH-200 |
200 |
120 |
80 |
3 |
0–15 |
500 |
SYH-400 |
400 |
240 |
160 |
4 |
0–15 |
900 |
SYH-1000 |
1000 |
600 |
400 |
7.5 |
0–12 |
1500 |
What are the advantages of three-dimensional motion mixer?
High uniformity: The mixing barrel performs composite movements such as translation, rotation, and rocking in three-dimensional space, so that the material produces a complex state of "rotational flow-translation-inverted falling", and the mixing rate can reach more than 99.9%. The uniformity error of drug content is lower than that of ordinary mixers.
No segregation phenomenon: The turbulent energy gradient generated during the movement can avoid the segregation and accumulation of material specific gravity caused by centrifugal force, ensuring that materials of different densities and particle sizes are mixed evenly.
High charging rate: The charging volume of the three-dimensional motion mixer can reach 80%-90% of the full volume of the barrel, significantly increasing the single mixing volume, reducing equipment floor space and operating costs.
Achieve gentle mixing and protect material integrity: The three-dimensional motion mixer mainly relies on the overall movement of the container to drive the mixing of internal materials, rather than strong shearing through high-speed rotating blades. This gentle mixing method minimizes mechanical damage to fragile and sensitive materials, and effectively reduces the risk of dust generation and material agglomeration.
Typical scenarios suitable for three-dimensional mixers
Due to its high uniformity mixing, large loading capacity, and easy cleaning, three-dimensional motion mixers are widely used in industries with high requirements for material mixing accuracy, hygiene standards, and production efficiency.
Mixing of APIs or Chinese medicine ingredients; Uniform processing of alloy powders and metal powders;
Compounding of food flavors, seasonings, etc.; Mixing of new materials such as battery materials and magnetic materials;
Occasions with high added value, difficult mixing, and requiring precise uniformity.
If you are looking for high mixing uniformity, large loading capacity, easy cleaning, and minimal damage to materials, a three-dimensional motion mixer is a better choice than a traditional mixer. If the materials are simple, the budget is limited, and the mixing accuracy requirements are not high, the traditional V-type and double-cone mixers are still cost-effective solutions.