Your location is: Home > Product center > Food conveyor belt
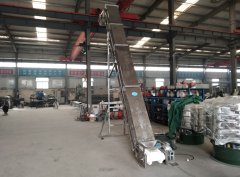
Food conveyor belt
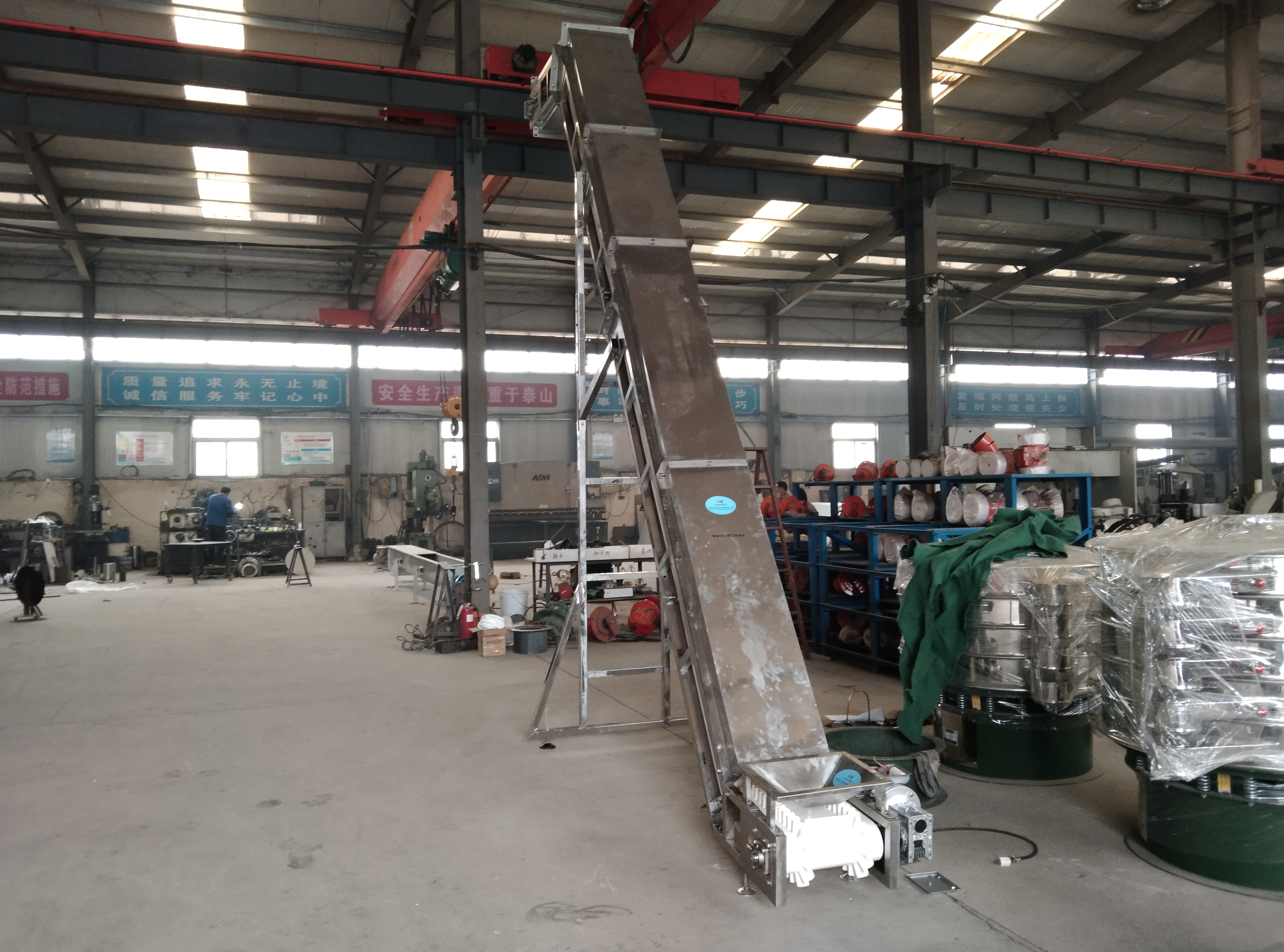
The operation of the equipment follows the closed-loop control principle: after the operator sets the conveying parameters on the control panel, the electrical control system sends instructions to the drive unit, and the motor drives the active roller to rotate through the transmission component. The belt forms continuous motion under the action of friction. When the material moves to the specified position with the belt, directional unloading is achieved through mechanical baffles, airflow sorting or gravity.
Under complex working conditions, the equipment can be configured with the following extended functions:
Dynamic weighing module: integrated with high-precision sensors to achieve real-time measurement during the conveying process;
Foreign matter detection unit: using electromagnetic induction or optical recognition technology to remove metal or non-standard materials;
Visual sorting system: through image acquisition and processing, identify and separate special-shaped or defective products.
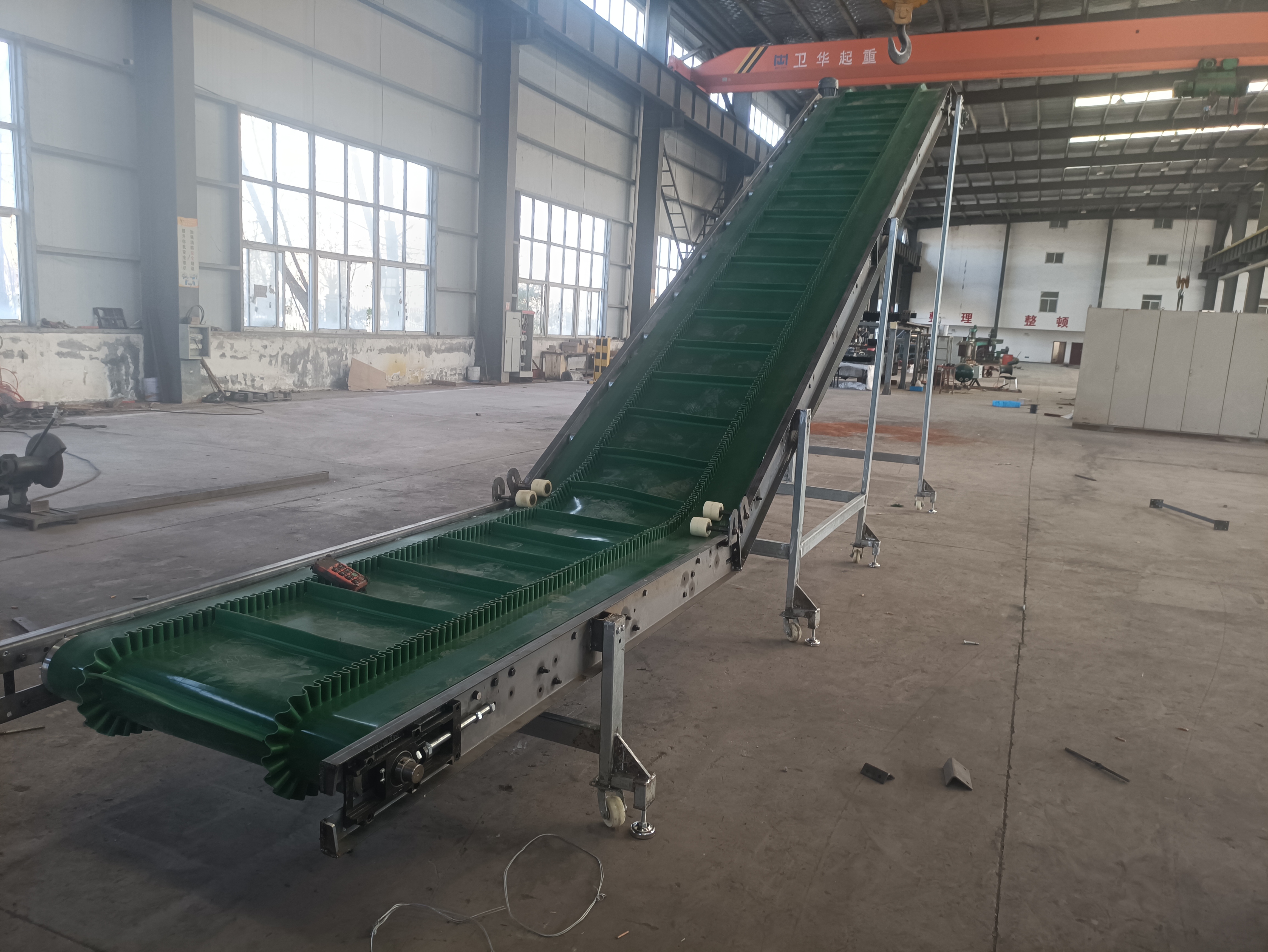
Conveyor belt system
The core components use modular plastic chain plates or PU/PVC food-grade belts. The former is connected by high-density polyethylene units through stainless steel hinges, with oil resistance, acid and alkali resistance, suitable for meat processing scenarios; the latter has a surface embossed pattern depth of 0.5-1.5mm, which enhances the friction coefficient and prevents material adhesion. The belt thickness is usually 3-8mm, and the tensile strength is ≥15MPa.
Drive and transmission mechanism
The main drive device uses a reduction motor and is equipped with a frequency converter to achieve soft start function. The drive shaft is made of 304 stainless steel with a surface roughness of Ra≤0.8μm to avoid metal debris contamination. The tensioning device adopts a spiral or gravity structure to ensure that the belt tension is maintained within the range of ±5% of the rated value.
Frame and support structure
The main frame is welded from 30×60mm aluminum profiles or 304 stainless steel square tubes, and the key parts are polished with a surface roughness of Ra≤1.6μm. The legs are equipped with adjustable feet to meet the height adjustment requirements of 0-500mm. The turning section adopts a conical roller design, and the minimum turning radius can reach 500mm, meeting the requirements of the U-shaped production line layout.
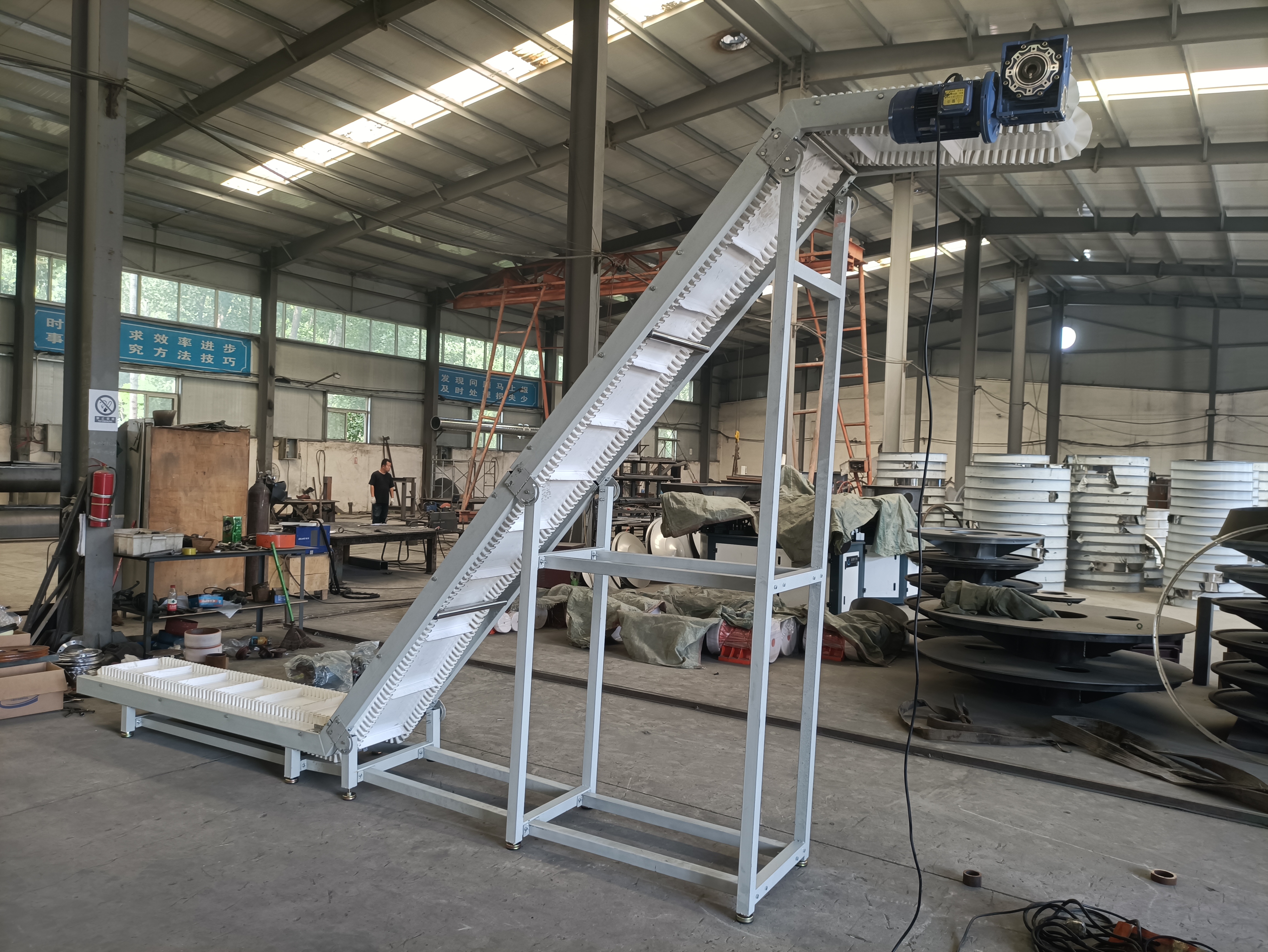
Application in the baking industry
In the bread production line, the equipment undertakes the task of dough transportation. The high-temperature resistant coated belt is used, and the segmented temperature control system is used to ensure the temperature accuracy of the fermentation process is ±1℃. The conveyor forms a linkage control with the proofing box and the tunnel furnace to realize the automation of the entire process.
Application in meat processing
Under low temperature and high humidity environment, the equipment uses a corrosion-resistant material frame, and the belt joints use a seamless welding process to eliminate cleaning dead corners. Equipped with an automatic lubrication system and food-grade lubricants to meet the temperature changes from -18℃ quick-freezing storage to 120℃ cooking line.
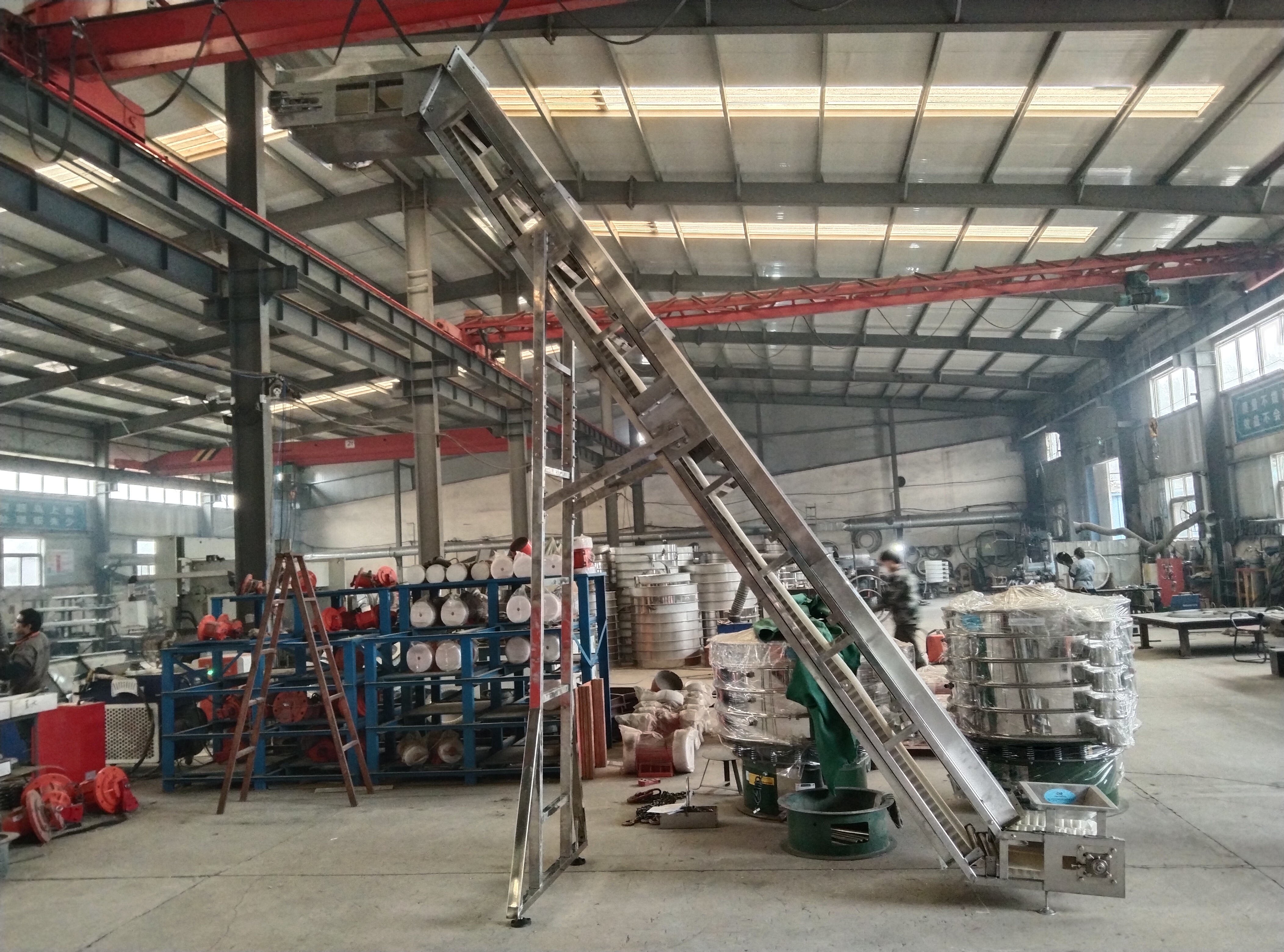
In the PET bottle conveying system, the equipment uses a low-friction belt and a lateral guide device to prevent the container from tipping over. The encoder is used to achieve synchronous control with the filling machine and labeling machine, with a positioning accuracy of ±1mm to ensure the efficiency of the packaging line.
Dairy product conveying application
For viscous materials such as yogurt, the surface of the equipment is polished to reduce the risk of material residue. The cleaning system integrates a disinfection module to perform sterilization simultaneously during the cleaning cycle to ensure that the microbial indicators meet the standards.
Sugested Products
Related news
Products Show
Sieving Machine
Conveying equipment
Bucket Elevator
Mixer
Packaging Machine
E-mail:
sale@xxdahan.com
WhatsApp:
+86 15836198876
Add:
Yanjin county forest park gate to the west 1000 meters north road