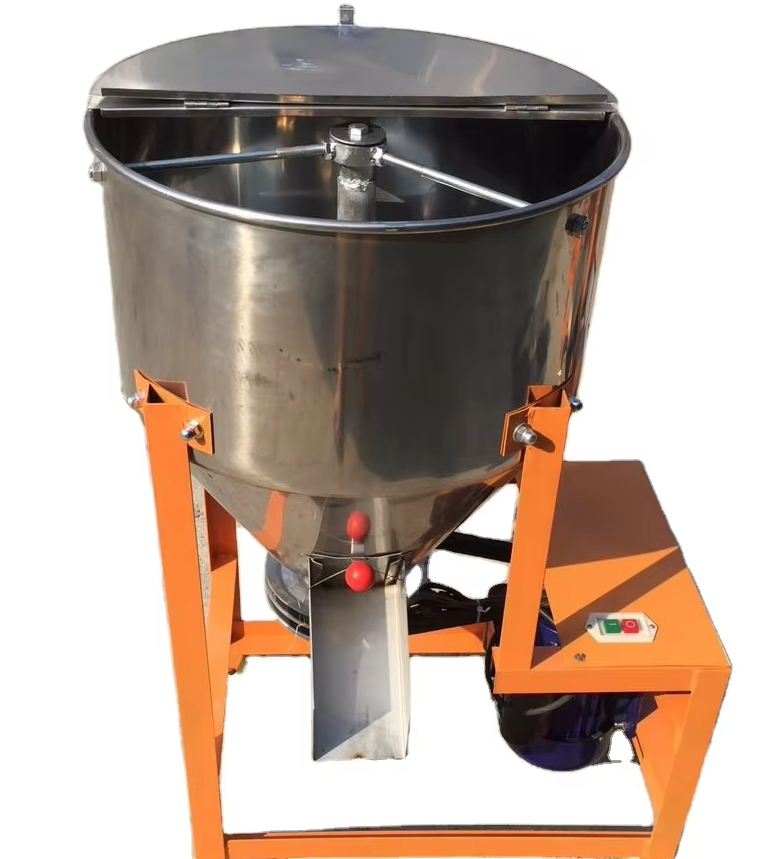
Poultry for chicken feed mixer
Poultry for chicken feed mixer is a mechanical equipment used to evenly mix various chicken feed raw materials, aiming to fully mix different ingredients (such as grains, protein feed, vitamins, minerals, etc.)
Dimensions 1000×600×1000mm ~ 3800×1600×2000mm
Rated capacity 100L ~ 6000L
One-time mixing volume 50kg ~ 3000kg
Mixing time 510 minutes (horizontal) / 12 minutes (double shaft)
What is a poultry for chicken feed mixer
Poultry for chicken feed mixer is a device used to evenly mix a variety of chicken feed raw materials (such as corn flour, soybean meal, bran, premix, trace additives, etc.) in a certain proportion. It is one of the core equipment in the chicken feed processing process. Its main purpose is to ensure that different nutrients are fully dispersed in the feed, so that poultry (such as broilers and laying hens) can take in balanced nutrition when eating, thereby improving growth rate, feed utilization rate and egg production performance.
What is the main function of poultry for chicken feed mixer?
The application of poultry for chicken feed mixer in feed processing is mainly concentrated in the uniform mixing of feed raw materials, which is one of the core sections in the entire chicken feed production process. The main functions of this equipment are:
① Evenly mix multiple ingredients. Chicken feed usually consists of more than 10 materials, including staple food (corn, soybean meal, etc.), minerals, trace elements, additives, premixes, etc. The mixer makes these ingredients evenly distributed through physical mixing to avoid uneven nutrition.
② Improve feeding effect and feed conversion rate: The higher the mixing quality, the more balanced the nutrition of the chickens, which helps to improve weight gain rate and egg production rate.
③ Shorten mixing time and improve efficiency: A reasonably selected mixer can complete the mixing of a batch of feed within 5 to 10 minutes, significantly improving production efficiency.
Classification of chicken feed mixers for poultry
Classification dimensions |
Vertical spiral mixer |
Twin-shaft paddle mixer |
Horizontal ribbon mixer |
Vertical cone mixer |
Picture |
|
|
|
|
Unit batch mixing volume |
Small (50–500kg) |
Medium to large (500–3000kg) |
Medium (100–2000kg) |
Small to medium (50–1000kg) |
Mixing time |
Long (10–15 minutes) |
Fast (30–120 seconds) |
Medium (5–10 minutes) |
Slow (15–20 minutes) |
Mixing uniformity |
General (C V≤10%) |
High (CV≤5%) |
Good (CV about 5–7%) |
High (CV≤5%, suitable for gentle mixing) |
Applicable material types |
Powdered, light, homogeneous materials |
Powder + trace additives, materials with large specific gravity differences |
Powdered materials + a small amount of particles or liquids |
Fragile materials with large specific gravity differences that require gentle mixing |
Application range |
Family farmers, small feed batching points |
Commodity feed mills, professional formula companies |
Farms, small and medium-sized feed mills, cooperatives |
High-end premix production, small batch multi-formulation production |
Working principle of poultry for chicken feed mixer
Various raw materials weighed according to the formula ratio enter the mixing drum through manual or automatic conveying devices.
After starting the motor, the reducer drives the mixing shaft to rotate. The mixing blades installed on the shaft apply shear force, impact force and friction force to the material, causing the material to produce complex movement in the mixing drum.
After a certain period of mixing (usually 3 to 10 minutes, depending on the machine model and material properties), all ingredients are fully mixed and evenly mixed. Open the discharge port, discharge the mixed feed, and enter the next process (such as granulation or packaging).
Structural composition of poultry for chicken feed mixer
Mixing drum: It is the main container for holding the materials to be mixed, usually a closed or semi-closed structure, with a smooth interior to reduce residue.
Mixing shaft and mixing blades/paddles: located inside the mixing drum, are the core components for achieving mixing. Depending on the model, there may be a single-shaft or dual-shaft design with various blade shapes (such as spiral, paddle, belt, etc.), which are used to push, shear and turn the feed.
Drive system: includes motor, reducer and transmission device, which are used to drive the mixing shaft to rotate.
Feed inlet and discharge port: The feed inlet is used to feed the weighed raw materials into the mixing drum; the discharge port is used to discharge the finished feed after mixing.
Model parameters of poultry for chicken feed mixer (taking horizontal ribbon mixer as an example)
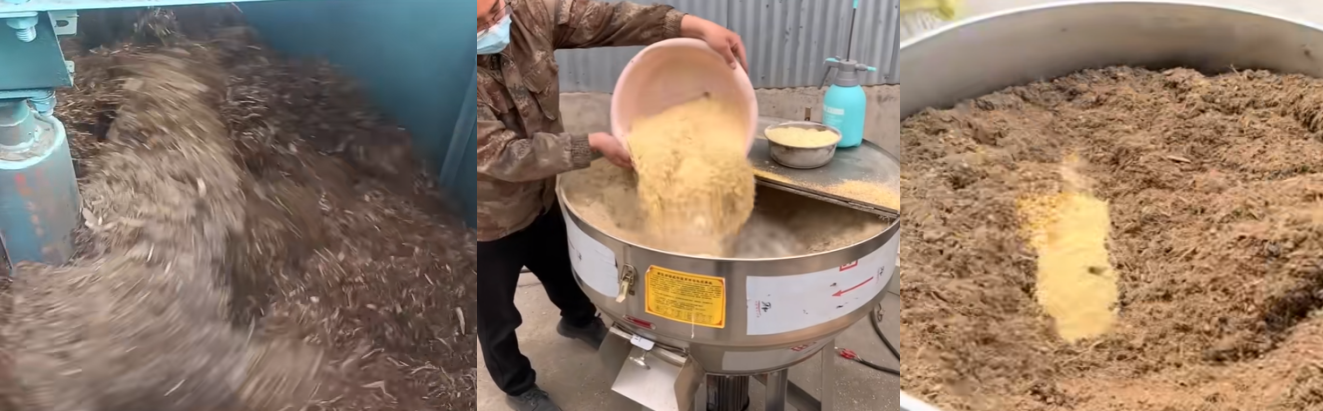
Model |
Volume (L) |
Amount of mixing at one time (kg) |
Mixing time (min) |
Motor power (kW) |
Dimensions (mm) |
Scope of application |
DH-J50 |
100 |
50 |
8–10 |
1.5 |
1000×600×1000 |
Suitable for family breeding and experimental mixing |
DH-J100 |
200 |
100 |
8–10 |
2.2 |
1200×700×1100 |
Small-scale farms |
DH-J250 |
500 |
250 |
8–10 |
4.0 |
1800×800×1200 |
Small and medium-sized breeders |
DH-J500 |
1000 |
500 |
8–10 |
5.5 |
2200×900× 1400 |
Feed workshop, cooperative |
DH-J1000 |
2000 |
1000 |
8–10 |
7.5 |
2600×1100×1500 |
Medium-sized feed processing point |
DH-J2000 |
4000 |
2000 |
10–15 |
11.0 |
3200×1400×1800 |
Scaled farm, large feed factory |
DH-J3000 |
6000 |
3000 |
10–15 |
15.0 |
3800×1600×2000 |
Used with continuous production line |
What is the process flow of chicken feed mixing
Raw material pretreatment: Cereals (corn, wheat, etc.) need to be crushed to 2-3mm particles; protein raw materials (soybean meal, fish meal) need to remove lumps; additives (vitamins, minerals) need to be premixed in proportion.
Preliminary mixing: Horizontal ribbon mixer: adopts a double-layer ribbon structure, the outer layer pushes the material to move axially, and the inner layer mixes in reverse, and uniformity can be achieved in 3-5 minutes (CV≤5%); vertical conical mixer: suitable for adding liquids (such as oils), and the material is mixed by spiral lifting and circulation, which takes 8-10 minutes.
Add trace ingredients: On the basis of preliminary mixing, the pre-prepared trace ingredients, such as salt, multivitamins, amino acids, etc., are evenly sprinkled into the mixer. Although these trace ingredients are used in small amounts, they are essential for the growth and health of chickens, and it is necessary to ensure that they are evenly distributed in the feed.
Fully stirring: Continue stirring for a certain period of time to fully mix all raw materials and additives. The length of stirring time will affect the mixing quality of the feed. Generally, the appropriate stirring time is determined according to the type of mixer and the characteristics of the feed.
Discharging and subsequent processing: After stirring, the mixed feed is discharged from the mixer. For powdered feed, it can be directly packaged and used to feed poultry; for feed that needs to be made into granules, subsequent processing procedures such as granulation and drying are also required.
Applicable materials for poultry for chicken feed mixer
Corn flour |
wheat flour |
rice bran |
Soybean meal |
rapeseed meal |
cottonseed meal |
Rice husk powder |
fish meal |
bone meal |
Stone powder |
salt |
wheat bran |
Vegetable oil |
molasses |
premix |
Vitamin additives |
antibiotic powder |
anthelmintic powder |
Beans |
trace element premix |
corn crushed finished granular material |
Application examples of poultry for chicken feed mixer
A small chicken farm: The chicken farm uses a vertical mixer to mix chicken feed. First, pour the main raw materials such as corn, soybean meal, and wheat bran into the mixer in a certain proportion, turn on the mixer, stir for 10-15 minutes, add a small amount of salt, multivitamins and other additives, and continue stirring for about 5 minutes to fully mix the various raw materials and additives. This mixing method is simple to operate and is suitable for small chicken farms. It can ensure the nutritional balance of feed and promote the healthy growth of chickens.
A large feed processing plant: When producing chicken feed, a horizontal mixer is used. First, crushed corn flour, soybean meal, fish meal and other raw materials are accurately weighed according to the formula and added to the mixer. At the same time, appropriate amounts of calcium hydrogen phosphate, methionine, multivitamins and other nutrients are added. The mixer runs at high speed to fully mix the various materials in a short time. Each batch of mixing takes only 3-4 minutes. After that, the mixed feed can be pelletized, dried and other subsequent processing steps, and finally made into granular chicken feed for large chicken farms.