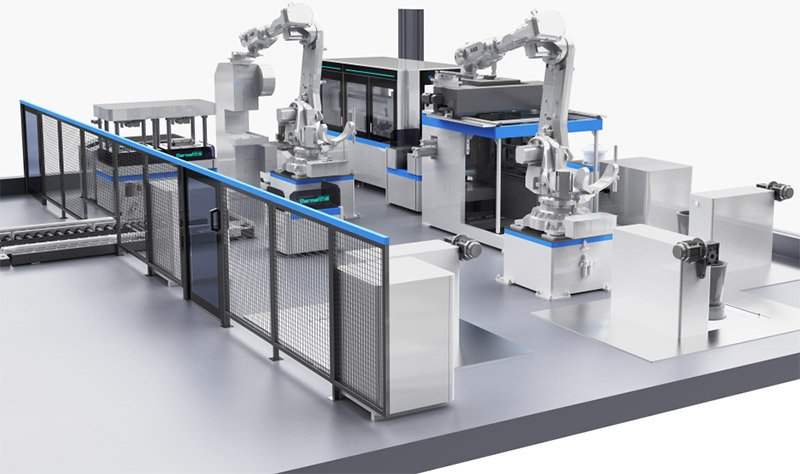
Fully automated silver ingot refining
Fully Automated Silver Ingot Refining System | 99.99% Purity & Zero Waste Solution Industry-Leading Automation for High-Yield Silver Recovery – AI-Driven, Eco-Safe & Cost-Efficient
What is Fully Automated Silver Ingot Refining?
In the era of Industry 4.0, fully automated silver ingot refining revolutionizes traditional metallurgy by integrating AI, robotics, and closed-loop recycling. Our system transforms raw silver scrap or ore into 99.99% pure ingots with zero manual intervention, eliminating human error and maximizing operational efficiency. Designed for refineries, jewelers, and electronics recyclers, this solution cuts costs by 40% while ensuring LBMA/ISO compliance48.
Key Features:
End-to-End Automation: From melting to molded ingots – no manual handling.
AI-Powered Impurity Control: Real-time spectroscopy detects contaminants (e.g., Pb, Cu) with ≤50ppm tolerance.
Energy Efficiency: 25% lower power consumption vs. conventional furnaces.
Why Choose Fully Automated Silver Ingot Refining?
Purity Guaranteed
Achieve ≥99.99% Ag purity through multi-stage electrolytic refining and centrifugal separation1.
AI adjusts chemical dosing (e.g., nitric acid) dynamically to minimize waste.
Zero Waste & Eco-Safe
Closed-loop filtration captures 100% airborne particles (OSHA compliant)8.
Slag recycling converts residues into reusable alloys.
30% Higher Productivity
Robotic arms handle 2-ton/day capacity with <0.1% material loss.
PLC-controlled smelting at 1,200–1,500K ensures uniform ingots14.
Global Compliance Ready
Pre-configured for LBMA, REACH, and EPA standards.
How Fully Automated Silver Ingot Refining Works?
Raw Material Loading: Conveyor belts feed silver scrap/ore into a 1,500K induction furnace (auto-sorted by XRF scanners).
AI-Driven Refining: Impurities removed via solvent extraction & electrowinning; AI optimizes chemical ratios.
Ingot Casting: Molten silver poured into custom molds (1kg–10kg) by robotic arms.
Quality Assurance: Laser assay verifies purity; defective ingots auto-recycled.
What are the applications of fully automated silver ingot refining?
Industry | Use Cases | Benefits |
Jewelry Manufacturing | Recycling scrap into premium-grade silver | 99.99% purity for fine craftsmanship |
Electronics Recycling | Recovering Ag from PCBs/switches | 98% yield from e-waste |
Industrial Refineries | Large-scale bullion production | 2-ton/day throughput |
Mining | On-site ore processing | Reduced transport costs |
Fully automated silver ingot refining case
Case Study: [ABC Precious Metals]
Challenge: Manual refining caused 15% material loss and inconsistent purity.
Solution: Deployed our PM-3000 Automated System.
Results: 99.992% purity achieved (LBMA certified); 40% lower labor costs with 24/7 operation.
How to Select the Right Fully automated silver ingot refining?
Capacity: Choose 50kg–5T/day models based on volume.
Purity Requirements: Opt for ≥99.99% if supplying LBMA markets.
Energy Source: Electric (cleaner) vs. gas (lower upfront cost).
Automation Level: Robotic integration vs. semi-automated.
After-Sales Support: Look for remote monitoring & 24/7 tech aid8.
Sugested Products
Related news
- Fully automated silver refining machine
- High-purity silver ingot production line
- Zero-waste silver recovery system
- Industrial-scale automated silver refinery
- Best silver ingot refining equipment
Sieving Machine
Conveying equipment
Bucket Elevator
Mixer
Packaging Machine
E-mail:
sale@xxdahan.com
WhatsApp:
+86 15836198876
Add:
Yanjin county forest park gate to the west 1000 meters north road