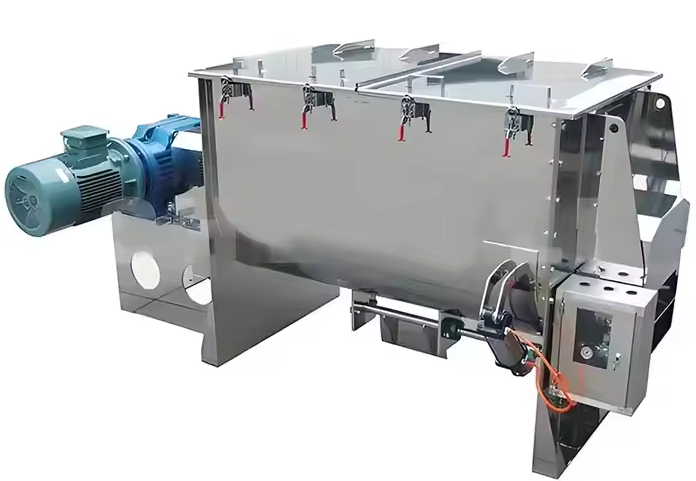
Ribbon dry mortar mixer
Ribbon dry mortar mixer is a commonly used mixing equipment in dry mortar production lines. It is mainly used to mix various dry powder materials, such as thermal insulation mortar, anti-cracking mortar, plastering mortar, bonding mortar, self-leveling mortar, etc.
Volume: 0.3~10 cubic meters
Mixing time: generally 3~10 minutes/batch
Motor power: 5.5kW ~ 37kW
Mixing uniformity: CV≤5% (depending on the material)
Processing capacity: 500kg/h ~ 10t/h
Material: carbon steel/stainless steel optional
What is a ribbon dry mortar mixer?
Ribbon dry mortar mixer is a horizontal mixing equipment used for mixing dry powder materials. It is often used to produce dry mixed mortar, putty powder, thermal insulation mortar and other building materials. Dry mortar is a non-sticky powder material with high specific gravity, good fluidity and easy dust emission, which has high requirements for mixing uniformity and mixing time.
The structure of the ribbon mixer is usually a U-shaped cylinder with double or multi-layer spiral blades inside. The outer ribbon pushes the material from both ends to the middle, and the inner ribbon pushes the middle material to both sides, forming an axial and radial composite flow, so that the material can be mixed quickly.
What is the difference between a double-layer ribbon dry mortar mixer and a multi-layer ribbon dry mortar mixer?
Both the double-layer ribbon dry mortar mixer and the multi-layer ribbon dry mortar mixer are a type of horizontal ribbon mixer, which are mainly used for efficient mixing of dry powder materials. The main differences between the two are reflected in the ribbon structure design, mixing efficiency, applicable materials and cost structure.
The double-layer spiral ribbon dry mortar mixer consists of two layers of spiral ribbons, which rotate in opposite directions on the same axis. In addition to the inner and outer layers, the multi-layer spiral ribbon dry mortar mixer may also add a third layer or even more layers or use spiral ribbons of special shapes (such as cones, paddles, etc.). The former uses the synergistic effect of the inner and outer spiral ribbons to form a convection circulation of the material in the cylinder, while the latter can add additional mixing units to further enhance the shear, dispersion, friction and convection of the material.
Double-layer spiral ribbons are more suitable for mixing conventional dry powder materials (such as ordinary dry mixed mortar, putty powder, etc.), with moderate mixing time and high uniformity (CV≤5%); multi-layer spiral ribbons have better mixing effects for materials with large differences in particle size and specific gravity (such as heavy aggregate + light additives), and multi-directional turbulence is conducive to avoiding "stratification" and "segregation" and other phenomena, which can further improve the mixing uniformity and shorten the mixing cycle (suitable for processes with higher precision requirements).
Working principle of spiral ribbon dry mortar mixer
The working principle of spiral ribbon dry mortar mixer is mainly based on the principle of bidirectional spiral convection mixing. Its core is to make the material move in the axial and radial directions at the same time through the inner and outer spiral ribbon blades arranged on the mixing shaft, so as to achieve efficient and uniform mixing effect.
The motor starts, driving the mixing shaft and the spiral ribbon blades on it to start rotating. The outer spiral ribbon pushes the material from both sides of the barrel to the center; the inner spiral ribbon pushes the central material to both sides; the two form axial convection mixing. When the spiral ribbon rotates, it drives the material to flip up and down, generating radial disturbance; light and heavy materials are sheared, diffused, and mixed; materials with large differences in particle size or specific gravity can also obtain better uniformity. During the entire mixing process, the material circulates in the horizontal direction and diffuses in the vertical direction to achieve all-round mixing.
Structural composition of spiral ribbon dry mortar mixer
Mixing barrel: usually a horizontal barrel, generally adopting a U-shaped or semi-open tubular structure, which can provide a large material mixing space, so that the material can be fully flipped and mixed in the barrel.
Mixing shaft and spiral ribbon: Double or multi-layer spiral ribbons are installed on the mixing shaft, and the shape and size of the spiral ribbons are designed according to different mixing requirements. The inner spiral ribbon and the outer spiral ribbon rotate in opposite directions. The inner spiral ribbon moves the material to both sides, and the outer spiral ribbon moves the material inward from both sides.
Driving device: including motor, reducer, etc., to provide power for the rotation of the mixing shaft. Through different transmission methods, such as direct connection, pulley connection, hydraulic coupling connection, etc., the power of the motor is transmitted to the mixing shaft, so that the spiral ribbon can rotate at a suitable speed.
Discharging device: Generally located in the center of the bottom of the cylinder, the common discharging method is the pneumatic large door structure, which is suitable for powder materials, fast unloading and no residue; for high-fineness materials or semi-fluid materials, manual butterfly valves or pneumatic butterfly valves can be used.
What are the advantages of spiral ribbon dry mortar mixer?
Efficient mixing and low energy consumption: The double helix structure enables the material to be evenly mixed in a short time, and the mixing uniformity is more than 95%. Compared with traditional mixers, energy consumption is reduced by 20%-30%.
Adapting to the characteristics of complex materials, it can handle sticky and thick materials (such as putty and rubber powder). After the spiral ribbon is equipped with a scraper, it can effectively prevent high-viscosity materials from sticking to the wall and agglomerating.
Operation stability and maintenance convenience: The equipment noise is less than 75dB, and the service life is up to 8-10 years. The modular design makes the spiral ribbon easy to replace and clean, and the maintenance cost is reduced by 30% compared with traditional models.
Technical parameters of spiral ribbon dry mortar mixer
Model |
Effective volume (m³) |
Batch output (kg/batch) |
Spindle speed (rpm) |
Motor power (kW) |
Overall dimensions (mm) |
Equipment weight (kg) |
LD-0.5 |
0.5 |
300–500 |
40–60 |
5.5 |
1800×800×1200 |
600–800 |
LD-1.0 |
1.0 |
600–1000 |
40–60 |
7.5 |
2200×900× 1300 |
900–1100 |
LD-2.0 |
2.0 |
1200–2000 |
40–60 |
11–15 |
2700×1100×1500 |
1300–1600 |
LD-3.0 |
3.0 |
1800–3000 |
40–60 |
18.5 |
3200×1200×1650 |
1800–2200 |
LD-4.0 |
4.0 |
2400–4000 |
40–60 |
22 |
3600×1 400×1700 |
2500–2800 |
LD-5.0 |
5.0 |
3000–5000 |
40–60 |
30 |
4000×1500×1800 |
3000–3500 |
LD-6.0 |
6.0 |
3600–6000 |
40–60 |
37 |
4500×1600×1900 |
3500–4000 |
LD-8.0 |
8.0 |
4800–8000 |
40–60 |
45 |
5000×1 800×2000 |
4000–4800 |
LD-10.0 |
10.0 |
6000–10000 |
40–60 |
55 |
5500×2000×2200 |
5000–6000 |
Dry mortar equipment | Dry mortar production line
Dry mortar equipment and dry mortar production line are the core components of producing various types of dry mortar. They mix dried and screened aggregates, cementitious materials and various additives in precise proportions to make ready-mixed powders that can be used directly. The dry mortar production line is a system that organically combines various dry mortar equipment to form a complete automated or semi-automated production process.
A typical dry mortar production line usually includes the following core links:
Raw material storage and transportation: Various powders and aggregates are stored in corresponding silos and transported to the next link through equipment such as elevators and screw conveyors.
Measuring and batching: According to the preset formula, various raw materials are accurately weighed by high-precision metering scales to ensure product quality.
Mixing and stirring: The measured materials enter the mixing and stirring machine (such as a ribbon mixer) for full and uniform mixing to achieve the required mortar properties.
Finished product storage and packaging: The mixed dry mortar is transported to the finished product warehouse and then bagged or bulked by the packaging machine for transportation and sales.
Central control system: The entire production process is monitored and operated by the central control system to achieve automated production.
What is the purpose of a ribbon dry mortar mixer?
Ribbon dry mortar mixers are widely used in the mixing of various dry powder materials in the building materials, chemical, metallurgical and other industries, especially for dry mortar production. In the construction field, it is often used to mix ordinary masonry mortar, plaster mortar, tile adhesive, putty powder, insulation mortar and other dry powder materials, suitable for small and medium-sized dry mortar production lines. Production and use. In the chemical industry, the equipment can be used to mix various powder additives, fillers and additives, such as talcum powder, silica fume, etc.
Commercial dry mortar station
Premixing on site at construction sites
Prefabricated component factory
Decoration material production enterprise