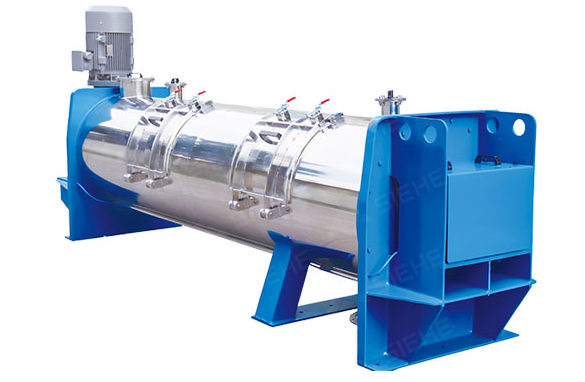
Powder for continuous mixer
Continuous mixers are widely used in the mixing of powders (dry materials such as powders and granules). The core of continuous mixers is continuous feeding, dynamic mixing, and uniform output, which are suitable for large-scale industrial production.
Particle size range: between 10μm and 2mm
Core advantages
No need to stop for loading/unloading, suitable for 24-hour automated production lines
Reduce stratification and agglomeration through screw, paddle and other designs
Mixing time can be shortened to 1-3 minutes, and uniformity can reach more than 85%
What is powder for continuous mixers?
Powder for continuous mixers refers to various types of powdered materials suitable for uniform mixing in continuous mixing equipment. Such powders usually have good fluidity, controllable particle size distribution and relatively stable physical properties. They can be stably fed into the mixing chamber through a continuous feeding system, and fully mixed and continuously discharged under the action of stirring mechanisms such as spirals, paddles or plows.
This continuous operation mode ensures that the material maintains a constant flow state and uniform residence time in the mixer, thereby significantly improving the uniformity and stability of the mixing effect. It can effectively overcome the common stratification, agglomeration or adhesion problems of powders during the mixing process, and is particularly good at handling powders with large differences in density and particle size or poor fluidity.
What are the three types of powder mixing?
Diffusion mixing: Mixing is achieved by the natural diffusion of powder particles and random arrangement during stacking; the mixing rate is slow, but the process is gentle, suitable for materials that are sensitive to particle shape; often used in medicines, foods and other occasions that require high particle integrity;
Equipment representatives: V-type mixers, double cone mixers and other intermittent equipment.
Convection mixing: Mechanical structures such as stirring blades, spiral ribbons, and coulters make large quantities of materials move as a whole to form macroscopic material flow for mixing; the mixing speed is fast and suitable for mass production; suitable for dry mortar, chemical additives, feed and other fields;
Equipment representatives: continuous mixers, coulter mixers, spiral ribbon mixers, etc.
Shear mixing: high shear force is used to make local slip, crushing or wetting between material particles, promoting micro-mixing; suitable for sticky powder, wet powder or liquid mixing, can break agglomeration and improve uniformity; used for adding spray, paste mixing, granulation pretreatment, etc.
Representative equipment: high-speed mixer, vertical shear mixer, high-speed granulation mixer, etc.
What is the difference between intermittent mixer and continuous mixer?
Project |
Batch mixer |
Continuous mixer |
Image |
|
|
Mixing method |
One-time feeding, one-time mixing, one-time discharging |
Continuous feeding, continuous mixing, continuous discharging |
Discharging method |
All-out discharge at one time |
Continuous discharging with stable flow rate |
Mixing uniformity |
Higher, suitable for products with high mixing precision requirements (such as medicine) |
Uniformity is slightly lower than intermittent type, suitable for products with relatively moderate uniformity requirements |
Production capacity |
Periodic, limited production capacity |
Sustainable feeding, high output and high efficiency |
Control complexity |
Simple control, flexible switching of formulas |
Requires matching precise continuous feeding and flow control system |
Material change and cleaning |
More flexible, easy to clean, suitable for small batch production of multiple varieties |
Difficult material change, suitable for long-term continuous production of a single product |
What are the advantages of powder for continuous mixers
Continuous material flow and shear: Continuous mixers keep materials in a dynamic flow state in the mixing chamber through continuous feeding and discharging. Combined with the efficient convection and shearing effect generated by internal stirring elements (such as paddles, spiral ribbons, coulters, etc.), materials can be continuously turned over to overcome the stratification trend caused by gravity.
Short and stable residence time: The residence time of materials in continuous mixers is usually short and evenly distributed. This means that there is not enough time for significant stratification between the time the materials enter the mixer and the time they are discharged.
Continuous flow reduces accumulation: Due to the continuous flow of materials, the residence time inside the mixer is short, and it is not easy to form long-term accumulation in certain areas, thereby reducing adhesion problems.
Efficient dispersion and mixing mechanism: Continuous mixers combine multiple mixing mechanisms such as convection, diffusion and shear to ensure that trace components can be quickly and evenly dispersed into the main material, even if their proportion is small, they can achieve high uniformity.
Working principle of powder for continuous mixers
Continuous mixers are used to process free-flowing powders or granular materials. The basic working principle is that the material enters the mixing chamber through a continuous quantitative feeding system, and is forced to be stirred and mixed under the action of rotating parts (such as spirals, blades, paddle wheels, etc.), and the material is continuously pushed to the outlet, realizing the flow process of "continuous feeding-continuous mixing-continuous discharge".
① Continuous feeding: Different powders are quantitatively and continuously fed into the mixer according to the set ratio.
② Internal stirring and mixing: The mixing chamber is equipped with spiral ribbons, paddles, double-axis or single-axis spiral elements. The materials are radially diffused and axially propelled under rotating stirring; different components are mixed with each other in continuous motion to achieve the set uniformity.
③ Continuous discharge: The mixed powder flows out continuously through the discharge port at the end and is connected to the next process, such as packaging, granulation, transportation, etc.; the discharge speed can be adjusted according to the process requirements to ensure the stability of continuous operation.
Structural composition of powder for continuous mixer
Inlet and outlet: The feed port is set with one or more groups, connected to the quantitative feeding system, and the components are continuously fed into the mixing chamber; the discharge port is located at the lower end or end of the equipment, connected to the subsequent equipment, and the discharge speed can be adjusted
Mixing chamber: Usually a U-shaped, cylindrical or conical shell, with a mixing element inside, which is the main space for powder mixing
Mixing element (stirring device): such as single-axis or double-axis spiral, paddle, plow, etc., determines the mixing effect and material flow state
Driving device: mainly composed of a motor and a reducer, driving Mixing element rotates or swings
The bracket and base support the whole machine structure to ensure stable operation
Technical specifications of powder for continuous mixer
Model |
Effective volume (L) |
Processing capacity (kg/h) |
Spindle power (kW) |
Mixing form |
Barrel size (mm) |
Applicable powder |
LCM-200 |
200 |
100~500 |
2.2 |
Single-axis spiral ribbon type |
Φ300×1000 |
Flour, calcium carbonate, etc. |
LCM-500 |
500 |
300~1000 |
4.0 |
Single-axis paddle type |
Φ450×1500 |
Feed additives, talcum powder, etc. |
LCM-1000 |
1000 |
500~2000 |
5.5 |
Double screw type |
Φ600×2000 |
Dry mortar, additive powder |
LCM-2000 |
2000 |
1000~4000 |
7.5 |
Double shaft paddle type |
Φ800×2500 |
Gypsum powder, lime powder |
LCM-3000 |
3000 |
1500~6000 |
11.0 |
Double shaft spiral type |
Φ1000×3000 |
Compound fertilizer powder, silicon powder |
LCM-5000 |
5000 |
2000~10000 |
15.0~18.5 |
Plow blade mixing |
Φ1200×3500 |
Heavy calcium, titanium dioxide, etc. |
LCM-8000 |
8000 |
3000~15000 |
22~30 |
Dual-axis high-efficiency paddle |
Φ1400×4000 |
High-capacity continuous mixing demand |
Application of powder for continuous mixer
Continuous mixers are widely used in industrial scenarios with high requirements for mixing efficiency and output in the field of powder, especially for mass production in industries such as building materials, chemicals, food, metallurgy, and feed. For example, in the production of dry mortar, the continuous mixer can continuously add different components such as cement, quartz sand, and lime powder in proportion to achieve rapid and uniform mixing, and continuously output finished products, greatly improving production efficiency.
In the production of chemical additives or compound fertilizers, for materials with different particle sizes and easy stratification, the continuous mixer effectively prevents segregation and achieves stable output through speed regulation and special structural design. In addition, this equipment is often used in the continuous mixing of seasoning powders, flour additives and other formula powders in the food industry to ensure accurate ratios and batch consistency.