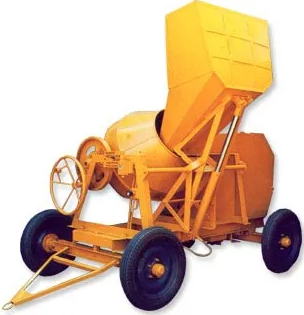
Concrete for small mixer machine
Concrete for small mixer machine is a small-scale construction equipment used to mix cement, sand, water and other additives to make concrete. It is suitable for home decoration, rural construction, road repair and other scenes
Moderate mixing efficiency: 0.1-0.5 cubic meters of concrete can be mixed each time
Mixing time: Generally, the mixing time for each batch is 1-2 minutes
Mobility: Some models (such as JZC series) are equipped with wheels for easy movement
What is a concrete for small mixer machine
Concrete for small mixer machine is a mechanical equipment suitable for small-scale concrete mixing operations, which can be accurately adapted to a variety of engineering scenes. Concrete is made of cement, sand, water and other raw materials mixed in a specific proportion. It has the characteristics of plasticity and high strength after coagulation and hardening. Concrete for small mixer machine is the key equipment to ensure that these characteristics can be fully utilized.
Through its unique mixing structure and operation mode, it can make all raw materials fully tumble and cross-mix in the mixing drum. Whether it is the uniform wet state required by plastic concrete or the tight combination required by dry and hard concrete, it can achieve an ideal mixing effect, effectively avoid problems such as segregation and agglomeration, and ensure the strength and durability of concrete.
Types of concrete for small mixer machines
① Self-falling mixer
Working principle: The inner wall of the mixing drum is equipped with radial mixing blades. When working, the mixing drum rotates around the horizontal axis. After the materials added to the mixing drum are lifted to a certain height by the blades, they fall due to gravity, thereby achieving a uniform mixing effect.
Scope of application: The structure is simple and generally suitable for mixing plastic concrete. It is often used in rural self-built houses, small road repairs and other projects.
② Forced mixer
Single horizontal shaft forced mixer: The rotating shaft arm is equipped with mixing blades. The materials in the mixing drum form a cross flow under the strong stirring of the mixing blades. It has strong mixing capacity and can be used to mix dry and hard concrete, lightweight concrete and various mortars. It is suitable for small projects with high requirements for concrete quality, such as small prefabricated component factories and small bridge construction.
Single-horizontal-shaft forced mixer: The rotating shaft blades mix at high speed, which is suitable for small prefabricated component plants, small bridge construction and other scenes with high requirements for concrete quality.
Double-horizontal-shaft forced mixer: The double-shaft blades mix crosswise, with better uniformity and efficiency. It is often used in small concrete mixing plants or standard brick and other building materials production, and can meet higher production requirements.
Vertical-shaft forced mixer: The mixing shaft is set vertically, with a compact structure and small footprint. It is suitable for laboratories or small sites with limited space, and has a significant forced mixing effect on materials.
Working principle of concrete for small mixer machine
Concrete for small mixer machines mainly rely on the rotation of the mixing drum to continuously lift, throw, flip and mix the materials in the drum, thereby achieving uniform mixing of cement, aggregate, water and other components. After the equipment is powered on, the motor drives the reduction device to operate, and drives the mixing drum to rotate through gears or chain transmission. During the rotation of the drum, the blades set inside roll the material along a certain trajectory, and through physical mixing, the concrete reaches a uniform state.
During the mixing process, the material is constantly subjected to shear, friction, convection and diffusion forces, so that different particles are fully in contact with each other, thereby improving the mixing effect. Some small mixers also have forward and reverse functions, which are convenient for unloading and cleaning.
Structural composition of concrete for small mixer machines
The mixing drum is the main space for material mixing. It is usually cylindrical and equipped with multiple mixing blades inside. The drum is mostly made of wear-resistant steel plates.
The mixing blades (or mixing arms) are fixed inside the drum or on the mixing shaft to push the material to roll, cut and other actions to achieve the purpose of mixing.
The motor provides the power required for the operation of the equipment, which is generally a single-phase or three-phase power supply.
The reducer converts the high-speed rotation of the motor into a low-speed and high-torque output to meet the load requirements of the mixing operation.
The transmission device includes gears, chains, belts, etc., which transmit power to the mixing drum or mixing shaft, which is common in drum mixers.
The bracket/frame is used to fix and support the entire equipment to ensure stability during operation.
The unloading device uses manual tilting cylinder, hand wheel, hydraulic or electric control discharge door to realize material unloading.
Technical specifications of concrete for small mixer machines
Concrete for small mixer machines are often used in small construction, rural house construction, municipal maintenance and other projects. They have the characteristics of simple structure, convenient operation and flexible transportation. Common models are distinguished by parameters such as mixing method, discharge capacity, motor power, etc.
1. Drum concrete mixer (such as JZC, JZM series)
Model |
Feed capacity (L) |
Discharge capacity (L) |
Productivity (m³/h) |
Motor power (kW) |
Mixing method |
Drive method |
JZC350 |
560 |
350 |
10~12 |
5.5 |
Free-fall type |
Gear transmission |
JZC500 |
800 |
500 |
20~25 |
7.5 |
Free-fall type |
Gear transmission |
JZM350 |
560 |
350 |
10~12 |
5.5 |
Free-fall type |
Friction wheel transmission |
JZM500 |
800 |
500 |
20~25 |
7.5 |
Free-fall type |
Friction wheel transmission |
2. Forced concrete mixer (such as JS series)
Model |
Feed capacity (L) |
Discharge capacity (L) |
Productivity (m³/h) |
Motor power (kW) |
Mixing method |
Scope of application |
JS350 |
560 |
350 |
10~12 |
7.5 |
Forced |
Construction site, mixing station |
JS500 |
800 |
500 |
20~25 |
18.5 |
Forced |
Small prefabricated component factory |
JS750 |
1200 |
750 |
35~40 |
30 |
Forced |
Commercial concrete station, small project |
What can concrete for small mixer machine be used for
Concrete for small mixer machine is widely used in various small construction sites, especially in rural house construction, urban and rural road repair, house foundation pouring, floor slab casting, courtyard hardening, ditch masonry and small bridge component construction. This type of project does not require much concrete, but has certain requirements for mixing uniformity and construction efficiency. Small mixers machine can quickly complete concrete mixing in a small space or temporary construction site due to their small size, flexible mobility and simple operation, avoiding the problems of low manual mixing efficiency and uneven quality.
For example, in the construction of self-built houses in rural areas, 350L drum mixers are often used to mix cement, sand and gravel, which can continuously supply 8 to 10 cubic meters of concrete per hour to meet the casting needs of multiple parts such as ground beams, columns, and walls; in municipal road repairs, small mixers machine can be operated with the construction team to quickly mix the repair concrete and reduce the time of traffic impact. For small foundation pouring of units such as electricity, gardens, and farms, small mixers machine can also achieve quantitative and efficient feeding, and are common tools for independently completing concrete mixing on site.
How to mix concrete with a small mixer machine?
Check the equipment: Make sure that all parts of the mixer are in good condition, especially the wiring of bearings, motors and electrical components should be firm, and the protection of zero or grounding resistance meets the regulations. Any abnormal situation needs to be resolved immediately.
Connect the power supply: Connect the mixer to a suitable power supply and perform a no-load test to ensure that the mixing drum or blades rotate in the same direction as the arrow on the drum.
Loading: Add the materials in the correct order. Usually, gravel is added first, then cement, and finally sand (or vice versa, sand first and cement last). Add water evenly to ensure that the concrete has suitable workability.
Start the mixer: Let the mixer run until the materials are completely mixed. This may take several minutes, depending on the model of the mixer and the proportion of the concrete.
Unloading: When the concrete is mixed evenly, you can pour the discharge port or tilt the mixing drum to unload the concrete.
Cleaning: After each use, the inside of the mixer should be cleaned in time to prevent the residual concrete from hardening and affecting the next use.
How much concrete can a small mixer machine produce?
The output of concrete for small mixer machines is affected by their capacity and working frequency. The following are common models and corresponding production capacity references:
Mixer model |
mixing volume per time (approximately) |
output per hour (approximately) |
JZC250 |
250 liters (0.25m³) |
5~7 cubic meters |
JZC350 |
350 liters (0.35m³) |
8~10 cubic meters |
JZC500 |
500 liters (0.5m³) |
10~15 cubic meters |
Note: The actual output is related to mixing time, operator efficiency, pause time, etc. If there are specific usage requirements (for example: rural house construction, road repair, indoor floor construction, etc.), you can choose a mixer model with appropriate capacity based on the project volume.