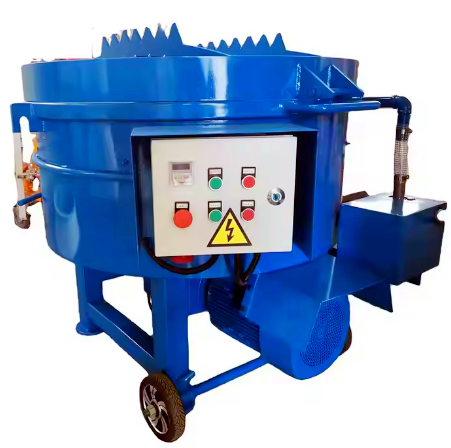
Refractory Mixer
The efficient mixing action can fully mix raw materials of different particle sizes and properties (such as aggregates, powders, binders, admixtures, etc.) to ensure the macro and micro uniformity of the materials
Mixing capacity: 100kg, 500kg, 250kg, 300kg, 500kg, 750kg, 800kg, 1000kg
Rotating speed: 33rpm-36rpm
Motor Power: 4kw-11kw
Feeding Height: 1100mm-1300mm
Dimensions (mm): 550kg-1010kg
What is a refractory mixer
Refractory materials are usually made of high melting point and high hardness granular raw materials (such as corundum, magnesia, etc.) mixed with binders and additives. They have the characteristics of high temperature resistance, thermal shock resistance, and erosion resistance. Their uniform mixing is crucial to product quality. The refractory mixer is a device designed for this type of special material. Through its unique mixing structure and process, it can efficiently achieve uniform mixing of materials.
It uses powerful mixing blades, combined with multi-directional motion trajectories, to perform composite movements such as shearing, flipping, and convection on high-viscosity, large-particle refractory materials, quickly breaking up material agglomerates, promoting full blending of different components, and avoiding local uneven components.
At the same time, the wear-resistant lining and corrosion-resistant materials of the mixer can resist the wear and chemical erosion of refractory materials during the mixing process, extending the service life of the equipment. The materials processed by the refractory mixer have high mixing uniformity and good particle dispersion, laying the foundation for subsequent molding and firing processes, and effectively improving the performance stability and quality reliability of refractory products.
What are the applicable scopes of refractory mixers?
Refractory mixers have a wide range of applications, covering a variety of refractory types and different industrial fields, as follows:
① Amorphous refractory materials: such as refractory castables, refractory ramming materials, refractory plastics, etc. These materials are usually composed of aggregates, powders, binders and admixtures, and need to be mixed evenly to ensure construction performance and use effects.
② Refractory mud: Joint materials used for refractory brick masonry, which need to be stirred to have good plasticity and adhesion to ensure the sealing and integrity of the furnace structure.
③ Raw materials for refractory prefabricated parts: When preparing raw materials such as refractory prefabricated blocks and refractory components, the components are evenly distributed through stirring to improve the strength and high temperature resistance of the prefabricated parts.
④ Special refractory materials: such as high-aluminum, silicon, magnesium, carbon and other refractory materials. According to the particle grading, density and chemical properties of different materials, the mixer can adjust the parameters to meet the mixing needs.
Structural composition of refractory mixer
The structural composition of refractory mixer is usually complex, but its core function is to achieve uniform mixing of materials.
The mixing barrel is the core part of the mixer, usually made of wear-resistant materials, able to withstand high temperature and high pressure to ensure uniform mixing
The mixing shaft is driven by a motor, and multiple mixing blades are installed on the mixing shaft to fully mix and mix the refractory materials
Motor: Provides power, usually a high-efficiency motor, which can ensure the stability and efficiency of the mixing process
Inlet and outlet: The inlet is used to put the raw materials into the mixing barrel, and the outlet discharges the mixed refractory materials
Control system: includes an electric control box and an operation panel, which is convenient for users to adjust parameters such as mixing speed and time.
Bracket and base: Support the entire mixer to ensure its stability, usually made of sturdy materials.
Working principle of refractory mixer
The working principle of refractory mixer mainly revolves around the adaptation of material properties and efficient mixing mechanism. Since refractory materials are mostly composed of high melting point particles, binders, etc., they have the characteristics of high particle hardness, high viscosity, and easy agglomeration. Its mixer usually adopts a multi-dimensional composite mixing structure. Taking the common planetary or double-shaft forced mixer as an example, the mixing blades (such as paddles, plow blades, etc.) are driven by a motor to achieve high-speed rotation, while the blades or mixing arms revolve along a specific trajectory, forming a compound motion mode of "shear + convection + flipping":
① Shearing effect: The high-speed rotating blades produce strong cutting of the agglomerated materials to break the agglomeration of particles;
② Convection motion: The revolution of the blades drives the materials to circulate in the mixing chamber, promoting the mutual penetration of materials of different densities and particle sizes;
③ Flipping and throwing: The specially designed blade angle and mixing chamber shape make the materials constantly thrown up and down during the movement to avoid local accumulation.
What are the advantages of refractory mixers
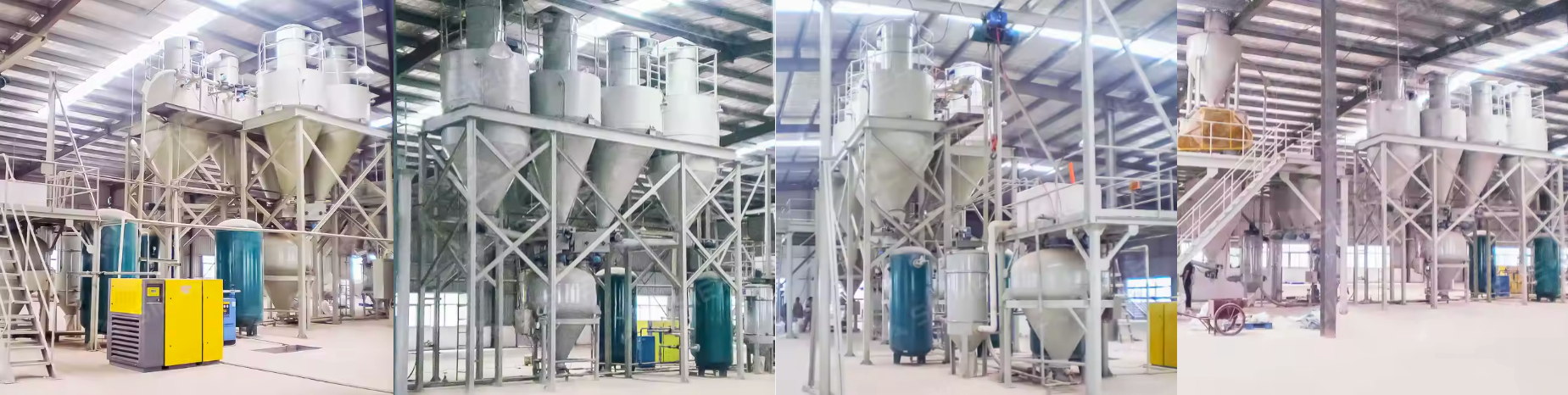
Solve the wear problem of high-hardness aggregates: The mixing blades and linings are welded with hard alloy or inlaid with ceramic linings, and the key parts of the blades are thickened to avoid the decrease of mixing uniformity due to wear.
Overcoming powder agglomeration and particle segregation: The countercurrent mixer generates high-intensity shear force through the reverse movement of the high-speed rotor (1200-2000 rpm) and the low-speed scraper, instantly tearing the powder agglomerates.
Solving the problem of refractory adhesion: The binder in the refractory material often has strong viscosity and is easy to adhere to the inner wall or blades of the mixer, resulting in a decrease in mixing efficiency. The refractory mixer is equipped with an efficient scraper system and optimized inner wall surface treatment (such as polishing or coating) to effectively scrape off the adhered materials, keep the mixing chamber clean, and improve the mixing efficiency.
Efficient mixing mechanism: Refractory mixers mostly use planetary or forced mixing structures, equipped with high-speed rotating mixing arms and multi-directional moving mixing blades. This design can generate strong shear force and convection effects, break the agglomeration between particles, promote the uniform mixing of aggregates, powders and additives of different particle sizes and densities, avoid stratification, and ensure the consistency of the chemical and physical properties of the mixture.
Technical parameters of refractory mixer
Item |
LRM100 |
LRM250 |
LRM500 |
Mixing capacity |
100kg |
250kg |
500kg |
Rotating speed |
33rpm |
34rpm |
36rpm |
Motor Power |
4kw |
7.5kw |
11kw |
Feeding Height |
1100mm |
1200mm |
1300mm |
Dimensions(mm) |
1400x1300x1100 |
1480x1380x1230 |
1700x1250x1350 |
Weight |
550kg |
650kg |
1010kg |
Note:Technical data may change due to technical progress, subject to modification without notice.
Application of mixer in refractory field
Refractory mixer is an indispensable core equipment in the field of refractory materials. Its application runs through the key links of various refractory preparations to ensure the excellent performance of the final product.
In the steel industry, blast furnace tapping channels, ladle linings, tundish linings, and heating furnace linings all require a large amount of high-quality refractory castables or ramming materials. The mixer is responsible for evenly mixing high-aluminum aggregates, corundum, sillimanite and other aggregates with cement, ultrafine powder, steel fiber and other binders and additives to ensure the fluidity of the castable and the strength and wear resistance after solidification.
In the cement and glass industries, the refractory linings of rotary kilns and melting furnaces have extremely high requirements for the high temperature resistance and corrosion resistance of the materials. The mixer is used to mix and prepare high-purity, high-performance magnesia-chrome bricks, spinel bricks or special castables.
In addition, in the fields of non-ferrous metal smelting, petrochemicals, and electric power, the mixer also plays a role in mixing various special refractory raw materials (such as silicon carbide, silicon nitride, zirconium oxide, etc.) in the preparation of refractory linings for high-temperature reactors, incinerators, boilers and other equipment to produce refractory bricks, prefabricated parts or amorphous refractory materials that meet specific working conditions.
Proof of Solutions for Our Wide Range of Products
Raw material mixing before the production of shaped refractory bricks
Preparation of amorphous refractory castables, spray coatings, ramming materials, etc.
Mixing of metallurgical furnace lining repair materials