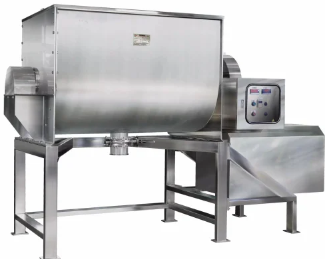
Chemical raw material mixer
Chemical raw material mixer is designed for chemical production, and achieves uniform mixing of chemical raw materials through mechanical force
Mixing capacity: 50L~10000L and above
Motor power: 1.5kW~30kW and above
Speed range: 20~150rpm adjustable
Mixing blade type: spiral blade, paddle blade, anchor blade, turbine blade, etc.
Mixing method: convection mixing, shear dispersion, mechanical flipping, etc.
Material viscosity range: 500~50000 mPa·s
Product description
Chemical raw material mixer is a professional equipment used for mixing, dispersing, dissolving or reacting various chemical raw materials in chemical production. Chemical raw materials have complex characteristics such as large viscosity difference, strong corrosiveness, flammability and reactivity, which requires the mixer to have targeted functions.
For low-viscosity raw materials, the mixer achieves rapid and uniform mixing through the shear force and turbulence generated by the high-speed rotation of the blades or turbines; for high-viscosity materials, special-structured mixers such as anchor-type and spiral-belt-type mixers can prevent material deposition and ensure that the material can be fully turned from the container wall to the center.
When handling corrosive raw materials, the mixer uses corrosion-resistant materials or special coatings to prevent the equipment from being corroded. With different types of mixers and structural designs, chemical raw material mixers can achieve convection mixing, diffusion mixing and shear mixing, ensuring that the raw materials have uniform composition and stable heat transfer in physical or chemical reactions, thereby improving the quality of chemical products and production efficiency.
What are the basic chemical raw materials?
Basic chemical raw materials are the foundation of the chemical industry, mainly including two categories: inorganic chemical raw materials and organic chemical raw materials.
Inorganic chemical raw materials, mainly inorganic acids, are widely used in the production of fertilizers, pesticides, explosives, etc.; inorganic alkalis are important raw materials for industries such as papermaking, textiles, printing and dyeing, and are used in the production of glass, soaps, detergents, etc.; salts are used in food processing, etc.
Organic chemical raw materials, such as ethylene, propylene, butadiene, benzene, toluene, xylene, etc. Ethylene is the core product of petrochemical industry and is used to produce a variety of plastics such as polyethylene and polyvinyl chloride; propylene is used to produce polypropylene, acrylonitrile, etc.; benzene is an important organic solvent and a raw material for synthetic resins, fibers, rubber, etc. Alcohols are mainly used to produce formaldehyde, acetic acid, etc.; aldehydes are used to produce resins, plastics, coatings, etc.
Classification of chemical raw material mixers
The types of chemical raw material mixers are placed in horizontal rows, and the classification dimensions (delivery volume, etc.) are placed in vertical columns
Ribbon mixers: usually used for mixing dry powders and granular materials. They consist of a U-shaped trough and a rotating agitator consisting of inner and outer spiral ribbons.
Paddle mixers: similar to ribbon mixers, but use paddles instead of ribbon agitators, and are also suitable for powders, granules, and sometimes pastes. Compared with ribbon mixers, paddle mixers have a gentler mixing action.
V-type blender/double cone blender: This type of blender is a tumbling type and is used to gently and evenly mix dry powders and granules. The container rotates, causing the material to tumble and mix.
Classification Dimension |
Ribbon Mixer |
Paddle Mixer |
V-Blender/Double Cone Blender |
Picture |
|
|
|
Mixed Material Type |
Dry powder, granules, pastes, slurries; Good adaptability to materials of different viscosities, especially good at mixing high-viscosity materials |
Dry powder, granules, block materials; Can also be used to mix a small amount of liquid or wet materials |
Dry powder, granules; Suitable for materials with good fluidity |
Conveying Volume |
Medium-high (50-5000L/batch) |
Medium-low (10-2000L/batch) |
Low to medium (5-1000L/batch) |
Mixing Principle |
In the horizontal cylinder, the inner and outer spiral belts rotate in opposite directions to mix the materials in radial and axial convection |
In the horizontal cylinder, the paddles rotate to push the materials for forced convection mixing |
The container rotates itself, and the materials are continuously dispersed and gathered under the action of gravity to achieve free-fall flip mixing |
Mixing Uniformity |
High, especially when mixing multiple components with large proportion differences. |
Medium to high |
High, especially suitable for materials that are sensitive to shear force, fragile or require gentle mixing |
Mixing time |
Relatively short, efficient |
Moderate to short |
Relatively long, but the mixing effect is gentle |
What does a chemical raw material mixer do?
The main function of a chemical raw material mixer is to fully and evenly mix two or more chemical raw materials (whether liquid, solid, gas or a combination of them) through mechanical action to achieve a specific production purpose.
①Achieve uniform distribution of materials: This is the most basic and most important function. Through stirring, raw materials of different properties and forms can be fully contacted and dispersed to form a uniform system at the macro and micro level, ensuring the consistency of the quality and performance of the final product.
②Promote physical changes: For example, accelerate the dissolution of solids, the dispersion of suspended particles, the emulsification of liquids, the absorption or desorption of gases, etc. Stirring can increase the contact area between materials and improve mass transfer efficiency.
③Accelerate chemical reactions: By evenly mixing the reactants, the mixer can increase the chance of collision between molecules, thereby increasing the reaction rate and conversion rate. In some multiphase reactions, stirring can also prevent the reactants from settling or stratifying, ensuring the continuous progress of the reaction.
④ Preventing precipitation and stratification: For mixtures containing solid particles or liquids of different densities, stirring can continuously stir the materials, prevent solid sedimentation or liquid stratification, and maintain the stability and uniformity of the system.
What are the shortcomings of chemical raw material mixers?
Insufficient mixing efficiency: For high-viscosity materials (such as heavy oils, resins) or heterogeneous systems (such as solid-liquid suspensions), traditional stirring paddle designs may cause uneven mixing due to insufficient shear force, requiring extended stirring time or increased energy consumption.
Equipment wear and maintenance: Since chemical raw materials are often corrosive, abrasive or high-temperature, long-term use may cause increased wear of components such as stirring blades and container walls, thereby increasing maintenance costs and downtime.
Mixing uniformity limitations: Although modern chemical raw material mixers are well designed, it is still challenging to achieve a completely uniform mixing effect for some special materials (such as extremely immiscible liquids or mixtures with greatly different solid particle sizes).
High initial investment cost: High-quality chemical raw material mixers, especially those customized equipment that can meet specific process requirements (such as corrosion resistance, explosion-proof, etc.), have relatively high initial purchase costs.
Technical parameters of chemical raw material mixers
Model |
Mixing capacity (L) |
Motor power (kW) |
Speed(rpm) |
Applicable material viscosity range (mPa·s) |
Remarks |
HT-SJB-100 |
50-100 |
1.5 |
60-140 |
500-5000 |
Small laboratory or pilot test |
HT-SJB-500 |
300-500 |
3.7 |
50-120 |
1000-8000 |
Small and medium-sized production |
HT-SJB-1000 |
800-1200 |
7.5 |
40-100 |
2000-15000 |
Large and medium-sized continuous production |
HT-SJB-3000 |
2500-3500 |
15 |
30-90 |
5000-30000 |
Large batches of high-viscosity materials |
HT-SJB-5000 |
4000-6000 |
22 |
20-80 |
10000-50000 |
Ultra-large capacity industrial production |
What can chemical raw material mixers be used for
Chemical raw material mixers are widely used in modern industry, and are used in almost all chemical production links involving fluids, powders or multiphase mixing.
In pharmaceuticals, mixers are used to mix active pharmaceutical ingredients and excipients to prepare uniform ointments, suspensions or tablet particles to ensure the consistency of drug efficacy; in the coatings industry, mixers are used to fully mix pigments, resins, solvents and various additives to produce paints and coatings with uniform color and stable performance to avoid stratification and agglomeration; in polymer material synthesis, such as the production of plastics, rubber, fibers, etc., mixers are responsible for the mixing and polymerization of monomers, initiators, catalysts and additives, controlling the reaction temperature and uniformity, and directly affecting the molecular weight distribution and physical properties of the final polymer; in addition, in the field of daily consumer products such as pesticides, detergents, and cosmetics, mixers are also indispensable for mixing active ingredients, emulsifiers, flavors, pigments, etc. to ensure the uniformity, stability and sensory experience of the product.
To help narrow down the range of the best mixers for your needs, you can consult our customer service and provide the following information:
What type of material do you want to mix? (e.g. liquid, powder, slurry, paste, gas or mixture)
Viscosity of the material? (e.g. watery, thick like honey, very paste-like)
What is the scale of your operation? (e.g. lab scale, pilot plant, industrial production)
What is the expected outcome of mixing? (e.g. simple mixing, dispersion, emulsification, dissolution, heat transfer)
Are there any specific requirements? (e.g. hygienic design, explosion protection, temperature control, vacuum operation)