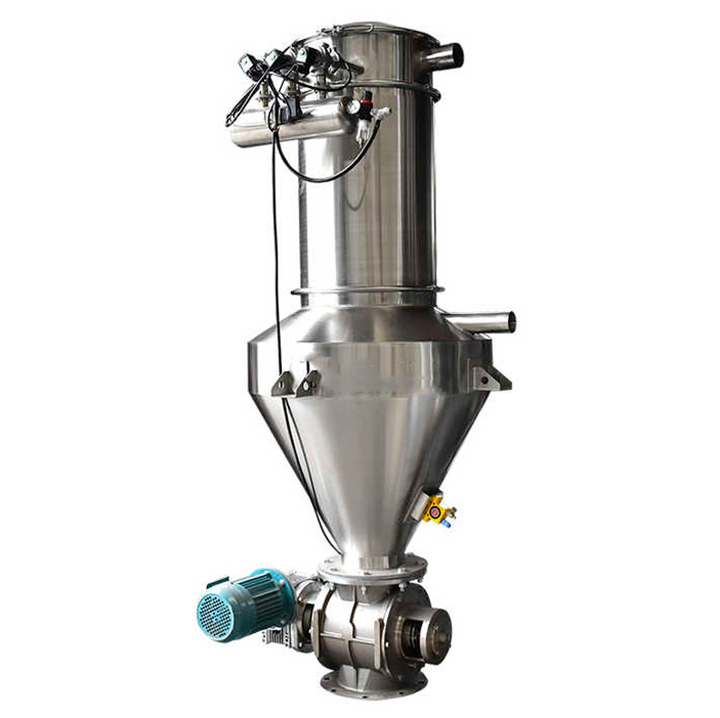
Continuous discharge type vacuum feeder
Continuous discharge type vacuum feeder is a fully automatic, dust-free powder/particle conveying equipment that uses the negative pressure principle to achieve continuous material suction, conveying, and discharge without manual intervention.
Power: 1.5-11 kW/customizable
Single bag size: 100X100X100 cm
Conveying capacity: 400-6000Koh
Conveying distance: 5-20 meters
Voltage: 220V/380V/415V or customized according to needs
Material: 304/316L stainless steel
Suction pipe can be extended: 2-30 meters
Applicable industries: pharmaceutical chemicals, food processing, plastics and rubber, new energy, building materials and metallurgy
What is a Continuous discharge type vacuum feeder?
Continuous discharge type vacuum feeder is specially designed for powder/granular materials. The working mode realizes 24-hour uninterrupted conveying, with a conveying capacity of 0.5-10t/h. It is equipped with an intelligent PLC control system, which improves efficiency by more than 60% compared with traditional equipment. It is suitable for chemical, pharmaceutical, food, lithium battery and other industries, and supports customized requirements such as explosion-proof, high temperature, CIP cleaning, etc. It has successfully served leading companies in the fields of lithium battery and pharmaceutical, and provides free trial and lifelong maintenance services to help companies upgrade to intelligence.
Continuous discharge type vacuum feeder advantages
The continuous discharge type vacuum feeder innovates industrial production with its high-speed, intelligent and environmentally friendly conveying capabilities.
Flexible layout: The conveying pipeline is like a flexible link, which can be freely planned according to the complex site layout. Whether it is multi-point feeding or multi-point unloading, it can be easily adapted.
Dust-free and airtight: The fully enclosed conveying environment is like putting on a solid "protective suit" for the material, eliminating the risk of material leakage and effectively preventing external pollutants from mixing in, which fully complies with GMP standards and the strict hygiene requirements of the food, pharmaceutical and other industries.
High degree of automation: With the help of PLC or sensor intelligent control, the equipment realizes the automation of the entire process from material absorption, transportation to discharge. This not only reduces manual intervention and labor costs, but also significantly improves the continuity and stability of production.
Easy to clean and maintain: The modular design concept makes the disassembly and assembly of the equipment simple and convenient. The continuous assistance of the backflush system greatly reduces the blockage of the filter element and reduces the maintenance frequency and cost.
Intelligent control: PLC+touch screen operation, supporting remote monitoring, fault alarm, and data traceability.
Continuous discharge type vacuum feeder type
Continuous discharge type vacuum feeders can be further divided into ordinary type and double-head type, which have their own characteristics in terms of structural design, working principle and applicable scenarios.
Ordinary continuous discharge type vacuum feeder: It is suitable for scenes with stable conveying volume, long distance and cost sensitivity, such as cement conveying in the building materials industry. Its advantages are simple structure, easy maintenance, low cost, and adaptability to a variety of materials.
Double-head continuous discharge type vacuum feeder: It is suitable for scenes with multi-equipment coordination, complex material distribution or high efficiency requirements, such as the lithium battery industry for accurate feeding of different equipment, and one discharge port can work while the other is maintained, ensuring production continuity and improving equipment efficiency.
Working principle of continuous discharge type vacuum feeder
The continuous discharge type vacuum feeder relies on the difference between vacuum negative pressure and ambient air pressure to achieve continuous and stable material conveying. Its operation process is as follows: the vacuum pump builds a vacuum environment in the conveying pipeline and the silo to form a negative pressure power, and sucks the material from the feeding point into the stainless steel closed pipe with a smooth inner wall; after the material enters the silo, the rapid filter separates the gas and material, and the purified air is discharged through the vacuum pump, and the material falls to the storage area under the action of gravity; at the same time, the compressed air pulse backwash system regularly cleans the filter to maintain its filtering performance.
Continuous discharge type vacuum feeder composition structure
The continuous discharge type vacuum feeder is mainly composed of five core parts: power system, conveying system, separation storage system, control system and auxiliary system. Each component works together to ensure efficient and stable material transportation.
Power system: The vacuum pump is the core power source. Common types include Roots vacuum pump, water ring vacuum pump and rotary vane vacuum pump. It is responsible for forming a stable negative pressure in the pipeline to provide power for material transportation.
Conveying system: It consists of a suction pipe, a conveying pipeline and a suction nozzle. It is made of stainless steel. The inner wall is smooth to reduce the resistance of material flow and has good sealing to prevent material leakage and outside air from entering.
Separation storage system: The silo is used to temporarily store the conveyed materials. It is mostly made of stainless steel with good corrosion resistance and strength. The internal design has structures such as guide plates to optimize material flow and prevent accumulation.
Control system: PLC is the control center, which monitors the operating status of the equipment in real time. According to the preset program and sensor feedback signal, it automatically controls the start and stop of the vacuum pump, the backflush cycle, and the opening and closing of the discharge valve.
Auxiliary system: The discharge valve is located at the bottom of the silo. Common types include butterfly valve, ball valve and rotary valve. Choose according to the material characteristics and production requirements to achieve continuous and stable discharge of materials.
Model parameters
Model |
Motor Power (KW) |
Conveying Capacity (Koh) |
HCSL - 1 |
1.5 |
400 |
HCSL - 2 |
2.2 |
600 |
HCSL - 3 |
3 |
1200 |
HCSL - 4 |
5.5 |
2500 |
HCSL - 6 |
5.5 |
3200 |
HCSL - 7 |
7.5 |
6000 |
HCSL - 10-6 |
7.5 |
6000 (When the conveying distance is 10 meters) |
HCSL - 20-5 |
11 |
5000 (When the conveying distance is 20 meters) |
What materials with characteristics can the continuous discharge type vacuum feeder convey?
The continuous discharge type vacuum feeder is widely suitable for materials with multiple characteristics due to its high-speed and stable conveying performance!
Dry materials: dry powders and granules (such as starch and sugar), non-sticky or low-sticky, not easy to agglomerate.
Low-humidity materials: materials with a moisture content of ≤5% (such as dehydrated vegetable powder and mineral powder), avoid moisture causing blockage of the conveying pipeline.
Slightly sticky materials: such as wet flour and certain food additives, need to be equipped with a vibration auxiliary module or a backflush device to prevent agglomeration in the silo.
Heat-sensitive materials: chocolate particles and some pharmaceutical intermediates can be prevented from deteriorating due to frictional heat generation by controlling the conveying temperature or using a low-temperature vacuum system.
Flammable/explosive materials: coal powder, aluminum powder, magnesium powder, etc., need to be equipped with explosion-proof vacuum pumps and anti-static pipes to meet ATEX and other explosion-proof certification requirements.
Continuous discharge type vacuum feeder application case
From intelligent transportation of lithium battery materials to aseptic production of pharmaceuticals, from quality upgrade of milk powder to precise processing of chemical pigments, continuous discharge type vacuum feeders break through industry pain points with customized solutions.
Lithium battery positive electrode materials: Lithium battery material manufacturers used to rely on manual feeding, which had problems such as low efficiency and difficulty in impurity control. The customized explosion-proof continuous vacuum feeder with nitrogen protection system (and high-sensitivity metal detector replaced 6 feeding stations at one stroke, saving 1.25 million yuan in labor costs annually.
Aseptic transportation of pharmaceutical raw materials: In order to meet GMP aseptic standards and strict audit requirements, API companies adopt customized solutions. The 316L all-stainless steel aseptic structure combined with the three-way ball valve CIP cleaning system and the weightless metering module not only controls the microbial content to <10CFU/m³, but also compresses the cleaning time between batches to 15 minutes.
Infant milk powder production: In order to solve the problems of protein denaturation, cross contamination and uneven formula caused by traditional transportation, low-shear Venturi transportation, dual-channel continuous design and online near-infrared monitoring system are innovatively adopted. After the transformation, the protein denaturation rate was greatly reduced from 3% to 0.5%, and 6 formulas can be switched with one button.
Chemical pigments: Faced with challenges such as pigment stratification, workshop explosion protection and system docking, enterprises have adopted pulsed airflow homogenization technology, ATEX certified explosion-proof units and OPC UA The communication interface has achieved a breakthrough. After the transformation, the mixing uniformity CV value was optimized from 7% to 2.5%, achieving zero safety accidents.
Why choose us as your supplier?
As a professional vacuum feeder manufacturer with many years of industry experience, Dahan Machinery has provided efficient and reliable powder conveying solutions to more than 3,000 customers in many countries around the world with a number of patented technologies and ISO9001/CE/ATEX certification. We have a leading R&D team that can customize special models such as explosion-proof and sterile, and strictly control the quality of digital factories, with a 24-hour rapid response lifelong service system, to ensure that customers get high-performance equipment with 30% energy saving and uniformity CV ≤ 3%, typical The customer cases show that it can help lithium battery companies reduce metal impurities by 90% and pharmaceutical companies increase production efficiency by 40%. We sincerely invite you to visit and create a win-win cooperation!
In modern industrial production, the efficiency and stability of material transportation directly affect the production capacity and quality of the entire production line. The traditional intermittent feeding method has been difficult to meet the production needs of high precision and high production capacity due to problems such as material residue, low transportation efficiency, and dust pollution. As a new generation of automated conveying equipment, the continuous discharge vacuum feeder is becoming the core equipment of the chemical, pharmaceutical, food, new energy and other industries with its high efficiency, closed and continuous operation characteristics.