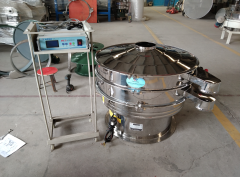
Ultrasonic Vibrating Screen Sieve for Fine Powder
What is Ultrasonic Vibrating Screen Sieve for Fine Powder?
Ultrasonic vibrating screen designed for fine powders breaks through the traditional screening bottleneck by integrating 38-40kHz ultrasonic technology and mechanical vibration system. The equipment is equipped with a variable frequency ultrasonic generator and an anti-stick coating screen, which effectively solves the problems of agglomeration and network blocking of 2μm-grade fine powder. It is suitable for high-difficulty materials such as pigments, carbon nanotubes, and pharmaceutical intermediates.
What is the Structure of Ultrasonic Vibrating Screen Sieve for Fine Powder?
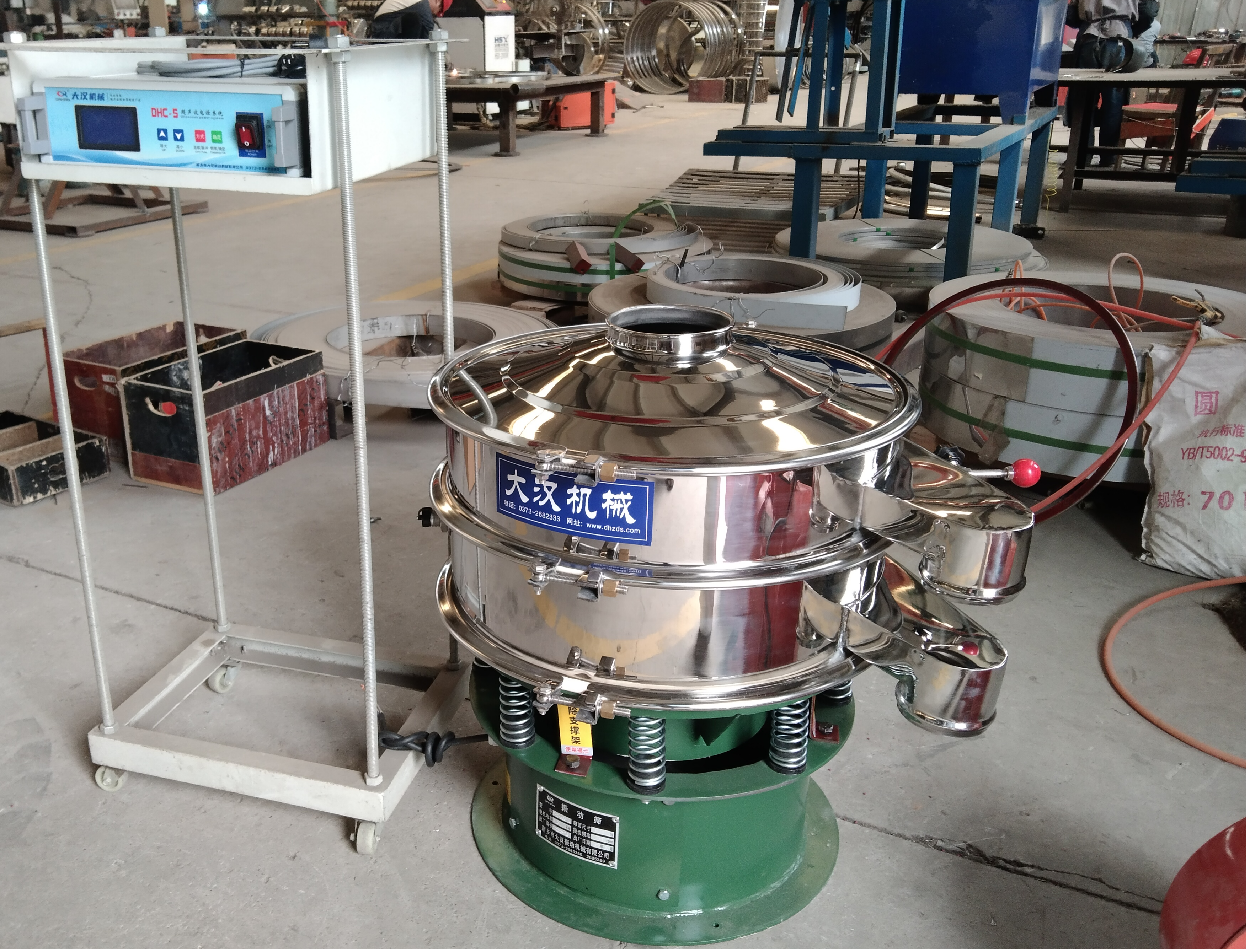
1. Multi-Layer Sieve Frames:2-5 removable frames with graded mesh (60-5000mesh/250μm-2μm) enable multi-level separation. Coarse layers (60-325目) use stainless steel for quartz sand/ceramic raw materials; ultra-fine layers (325-2000 mesh) employ high-precision alloy mesh for battery cathode materials/catalysts;nano-grade layers(2000-5000mesh) have ultrasonic-embedded sieves for graphene/nano-TiO₂, achieving 2μm control via ultrasonic dispersion.
2. Dual Vibration System: A mechanical base generates 3D linear vibrations (50-300Hz, 0.1-1.5mm amplitude) for material transport, while ultrasonic transducers add 38-40kHz high-frequency vibrations to sieve surfaces, creating a "sonic lift" that reduces mesh blinding by 95% for cohesive powders like carbon black.
3. Material-Resistant Design: Teflon/PTFE anti-adhesion coatings prevent particle sticking; 316L stainless steel/titanium alloy ensures corrosion resistance for wet/corrosive environments.
4. Modular Flexibility: Quick-release frames allow 3-minute mesh replacement, and an adjustable screening angle optimizes flow for nano-powders/ceramic granules, handling 50-500g samples with precision.
What is the Working Principle of Ultrasonic Vibrating Screen Sieve?
The device integrates mechanical vibration with ultrasonic energy to achieve fine powder separation:1. Dual-vibration source drive: A traditional vibration motor generates 3D linear vibrations (frequency 50-300Hz, amplitude 0.1-1.5mm), while an ultrasonic transducer superimposes 38-40kHz high-frequency vibrations on the sieve surface.
2. Ultrasonic anti-blinding effect: High-frequency ultrasonic waves create a "sonic cushion" on the sieve mesh, preventing fine particles from adhering or blocking the apertures. This allows even highly cohesive powders (e.g., carbon black) to pass through smoothly.
3. Precision grading process: Materials enter the top sieve frame and are pushed forward by mechanical vibration. Simultaneously, ultrasonic waves disperse agglomerates, enabling particles smaller than the sieve aperture to pass through layer by layer, while larger particles are discharged from the outlet.
4. Data-driven screening: Advanced models feature real-time monitoring of ultrasonic power and vibration parameters, automatically adjusting to maintain screening efficiency and generate particle size distribution reports with errors ≤1.5%.
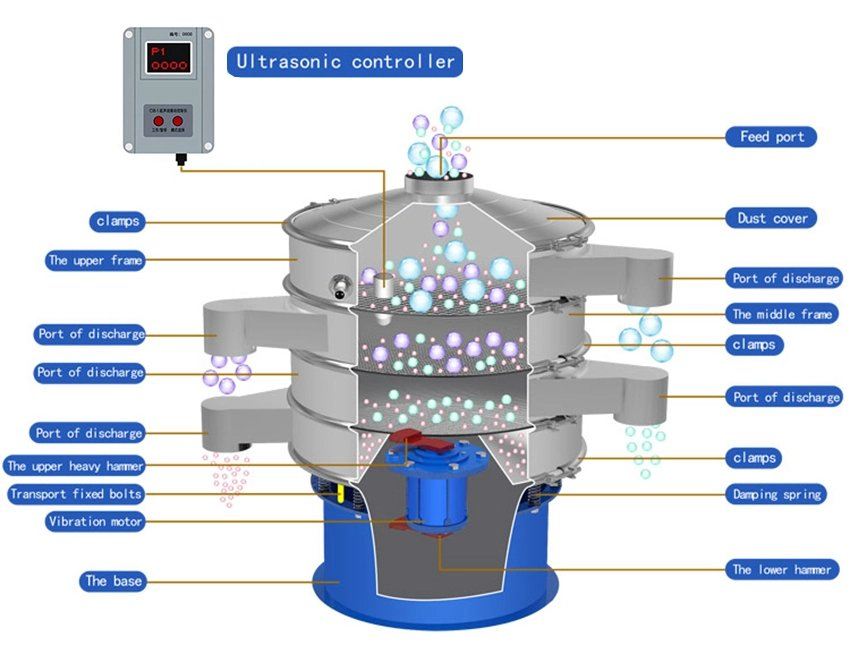
What are the Core Advantages of Ultrasonic Vibrating Screen Sieve?
This technology stands out for its breakthrough in fine powder screening, combining efficiency, precision, and adaptability:1. Exceptional fine powder handling: Compared to conventional vibrating screens, it increases screening efficiency for ≤50μm powders by 120%, with a screening accuracy of ±1.5%. Ultrasonic waves eliminate 95% of mesh blinding, even for materials with a moisture content of ≤8%.
2. Multi-material compatibility: Anti-adhesion coatings (Teflon/PTFE) and corrosion-resistant materials (316L stainless steel) support screening of corrosive, high-purity, and sticky powders. The ultrasonic system is adjustable for different materials, from hydrophobic silica to hydrophilic pharmaceutical excipients.
3. Intelligent operation & low maintenance: One-key activation with automatic ultrasonic power adjustment; quick-release sieve frames enable 3-minute mesh replacement. The ultrasonic generator has a service life of ≥10,000 hours, and the vibration system features the self-diagnosis function, reducing downtime by 70%.
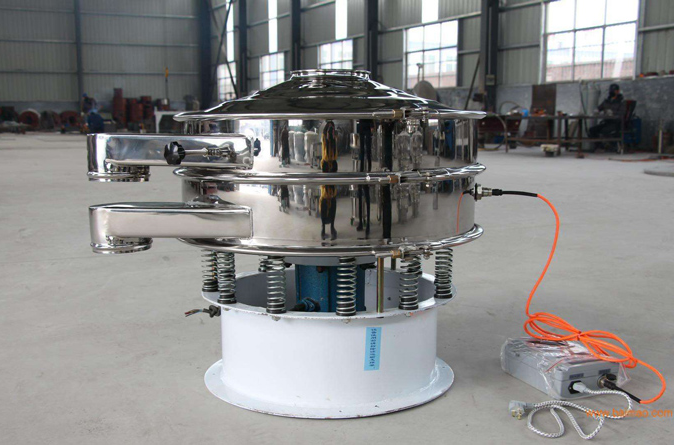
Where is Ultrasonic Vibrating Screen Sieve applied?
With its excellent ultra-fine powder handling capability and material adaptability, ultrasonic vibrating screens have become the core equipment for quality control and research and development in the high-tech field, playing a key role in nano-scale material screening.1. Pharmaceuticals: Screening of nano-crystalline APIs (e.g., paclitaxel particles ≤200nm) and lyophilized powders, ensuring uniform particle size for improved bioavailability. Excipient screening (e.g., lactose ≤50μm, residue on 300 mesh ≤1%).
2. Electronics & New Materials: Grading of graphene sheets (≤5 layers) and carbon nanotubes (diameter 10-50nm), supporting the production of high-performance conductive inks. Lithium battery cathode materials (e.g., LFP powders with D50=5-10μm for enhanced battery cycle life).
3. Chemical & Cosmetics: Pigment grading (e.g., titanium dioxide particles ≤100nm for high-gloss coatings) and nano-mica screening for cosmetics, ensuring texture and color uniformity.
4. Nanotechnology R&D: Laboratory-scale screening of quantum dots, nano-ceramics, and other advanced materials, enabling precise control of particle size distributions for property optimization.
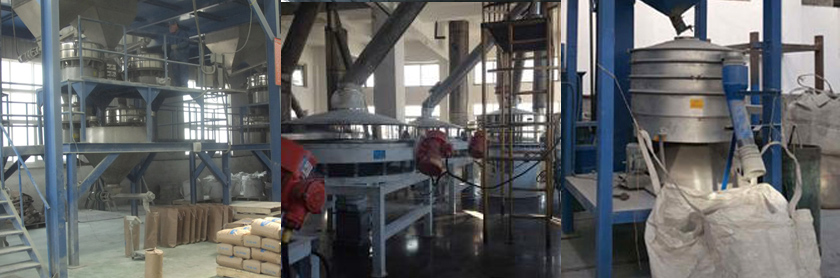