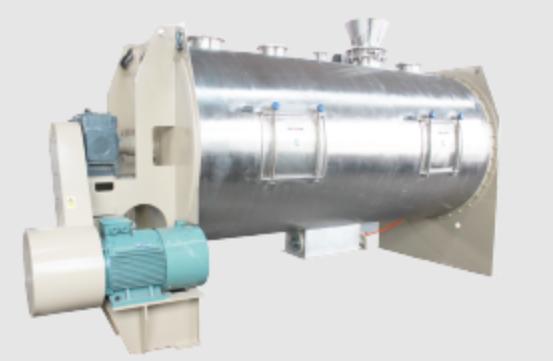
Horizontal ribbon mixer
Horizontal ribbon mixer is an industrial equipment commonly used for mixing powder, granules, paste or a small amount of liquid. It is widely used in chemical, food, pharmaceutical, building materials, feed and other industries.
Material specific gravity: ≤5g/cm³ Production capacity 100-30,000L
What is a horizontal ribbon mixer?
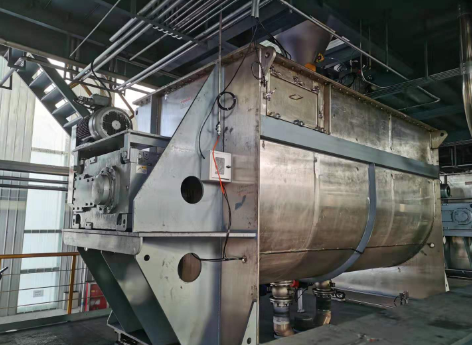
The horizontal ribbon mixer is suitable for mixing powders with powders, particles with powders, and powders with a small amount of liquid. It is widely used in chemical, pharmaceutical, food, feed, plastics and building materials industries. The machine has wide adaptability to mixtures, can mix viscous materials evenly, can keep the particles intact as much as possible, and can mix materials with a ratio difference of 1:1000-10000 well.
Applicable materials for horizontal ribbon mixer
The horizontal ribbon mixer is suitable for various powders, slurries, and granular materials with a specific gravity below 5g/cm³, a liquid content below 70%, and fluidity; such as pharmaceutical intermediates, food seasoning powders, pesticides, active dyes, paint putty, anti-cracking mortar, real stone paint, and more than a thousand other materials.
Powder mixing: flour, milk, fertilizer, flour, etc.
Feed, coffee beans, plastic granules, mixed granules, etc.
Thickener: putty powder, dry mortar, mixed additives, etc.
Liquids that can be added: flavoring, oil spraying, spraying, etc. (liquid spraying device is required)
Working principle

The horizontal ribbon mixer drives the shaft to stir and rotate through the motor. A double-layer ribbon is installed on the shaft. The outer ribbon will actively replenish from the middle to the middle, and the inner ribbon will actively replenish from the middle to the middle, thereby forming convection mixing.
The structure can achieve high efficiency and high uniformity mixing effect, which is particularly suitable for viscous or gradient increment inventory.
Structural composition
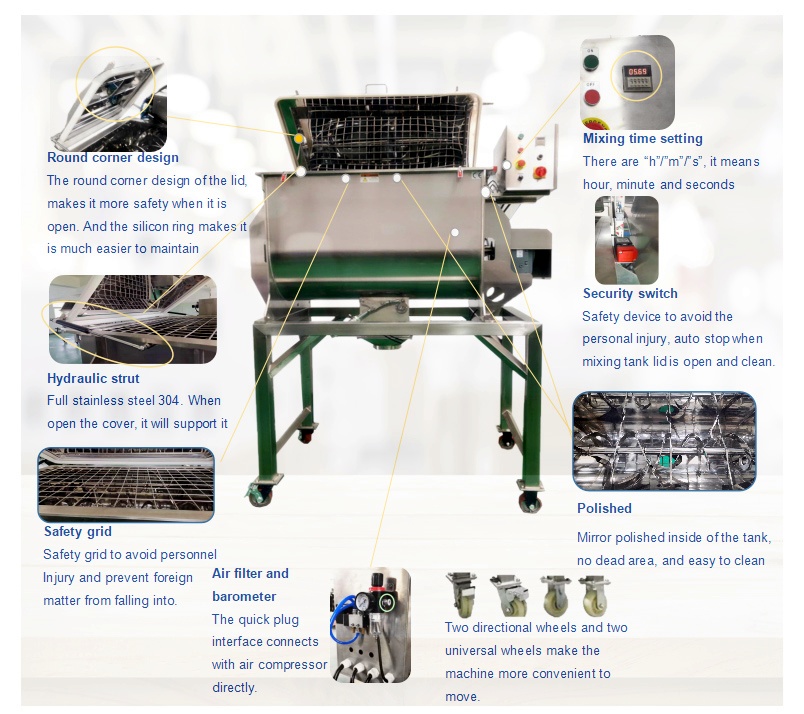
The horizontal ribbon mixer is mainly composed of the following parts:
U-shaped container: a horizontally placed cylinder with a smooth interior to reduce material residue, mostly made of stainless steel or carbon steel (anti-corrosion treatment).
Spiral agitator: It consists of two layers of inner and outer spiral ribbons. Usually the outer spiral pushes the material to one end, and the inner spiral pushes in the opposite direction to form convection mixing.
Transmission device: including motor, reducer, coupling, etc., drives the spiral belt to rotate at a low speed (usually at a speed of 20-60 rpm).
Discharge system: There is a pneumatic/manual discharge door at the bottom, and the mixed materials can be discharged quickly to reduce dead angles.
What are the advantages of horizontal spiral belt mixers?
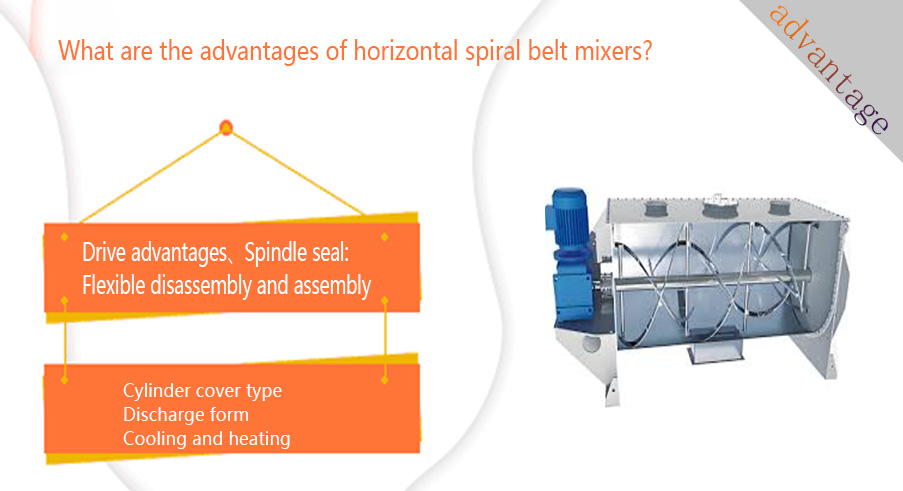
Drive advantages: Standard products are directly driven by gear reducers, with large torque, high reliability and low noise. Large equipment uses gear reducers plus belt drive to protect transmission components in case of unexpected situations.
Flexible disassembly and assembly: The spiral belt main shaft is flange-connected to the drive shaft and can be quickly disassembled when maintenance or replacement of the stirring shaft type is required. The flexible disassembly and assembly design allows the U-shaped cylinder to be completely welded with the two end plates to avoid the accumulation gap caused by the connection of the cylinder and reduce residue.
Cylinder cover type: Compared with other types of mixers, the cylinder cover of the horizontal spiral belt is more flexible and can be made fully open, half-open, and fully closed. The fully open one is suitable for occasions with high cleaning requirements. It is supported by gas springs, which is convenient and safe.
Discharge form: The discharge form is generally a pneumatic flap valve. The arc valve is tightly embedded in the barrel and flush with the inner wall of the barrel. There is no material accumulation and mixing dead corner. The reliable side strip seal ensures that there is no leakage during frequent switching.
Cooling and heating: A jacket can be added outside the mixer barrel, and the material can be cooled or heated by injecting cold and hot media into the jacket; industrial water is generally pumped in for cooling, and steam or electric heating heat transfer oil can be introduced for heating.
Spindle seal: A new balanced combined air seal plus packing seal is used. When mixing ultra-fine powder, this seal can increase air tightness and effectively block the flow of gas and powder inside and outside the barrel.
Common specifications and models
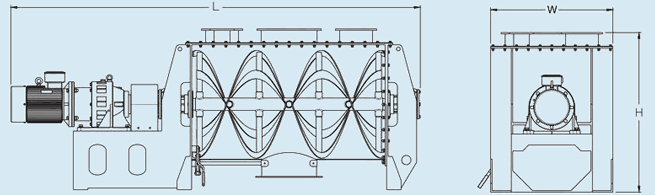
Model |
Motor power (kw) | Speed (rpm) |
Barrel thickness (mm) |
Mixing volume (L) | Dimensions (mm) | Equipment weight (kg) | ||
Length | width | height | ||||||
DH-0.1 | 3 | 60 | 4 | 30-60 | 1500 | 500 | 700 | 400 |
DH-0.2 | 4 | 60 | 4 | 60-120 | 2000 | 600 | 900 | 600 |
DH-0.3 | 5.5 | 41 | 4 | 90-180 | 2000 | 700 | 1000 | 800 |
DH-0.5 | 7.5 | 41 | 5 | 150-300 | 2500 | 800 | 1400 | 1200 |
DH-1 | 11 | 33 | 5 | 300-600 | 2700 | 1000 | 1450 | 1800 |
DH-2 | 15 | 33 | 5 | 600-1200 | 3400 | 1200 | 1700 | 2300 |
DH-3 | 18.5 | 33 | 6 | 900-1800 | 3800 | 1300 | 1950 | 3200 |
DH-4 | 22 | 26 | 6 | 1200-2400 | 4100 | 1400 | 2000 | 4000 |
DH-5 | 30 | 26 | 6 | 1500-3000 | 4200 | 1500 | 2000 | 4500 |
DH-6 | 37 | 26 | 6 | 1800-3600 | 4500 | 1700 | 2100 | 6000 |
DH-8 | 45 | 20 | 6 | 2400-4800 | 5000 | 1800 | 2200 | 7000 |
DH-10 | 55 | 20 | 8 | 3000-6000 | 50 00 | 1900 | 2500 | 8000 |
DH-15 | 90 | 20 | 8 | 4500-9000 | 6500 | 2100 | 2800 | 9800 |
DH-20 | 110 | 18 | 8 | 6000-12000 | 7500 | 2400 | 3000 | 13000 |
DH-30 | 132 | 16 | 10 | 9000-18000 | 9000 | 2600 | 3500 | 18000 |
Application of horizontal ribbon mixer
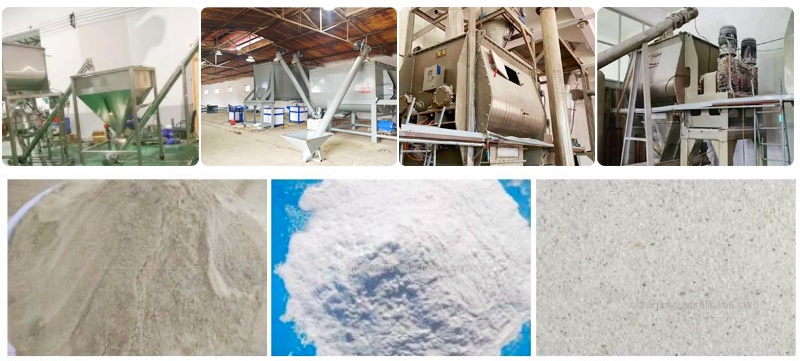
Plastic and rubber processing: used to mix plastic particles, rubber additives (such as carbon black, vulcanizers), fillers (such as calcium carbonate, talcum powder), etc., to ensure that each component is evenly dispersed and improve product performance.
Fertilizer and pesticide preparation: mixed nitrogen, phosphorus and potassium compound fertilizers, organic fertilizers, pesticide powders (such as insecticides, fungicides), especially suitable for mixing viscous materials (such as organic fertilizers containing liquid fertilizers).
Livestock and poultry feed production: mixed energy feed (such as corn flour), protein feed (such as soybean meal), mineral feed (such as bone meal) and premixes to ensure balanced nutrition.
Powder food processing: mixed flour, starch, seasonings (such as hot pot base, soup), nutritional powders (such as protein powder, infant formula powder), etc., to ensure uniform ingredients.
Sugested Products
Sieving Machine
Conveying equipment
Bucket Elevator
Mixer
Packaging Machine
E-mail:
sale@xxdahan.com
WhatsApp:
+86 15836198876
Add:
Yanjin county forest park gate to the west 1000 meters north road